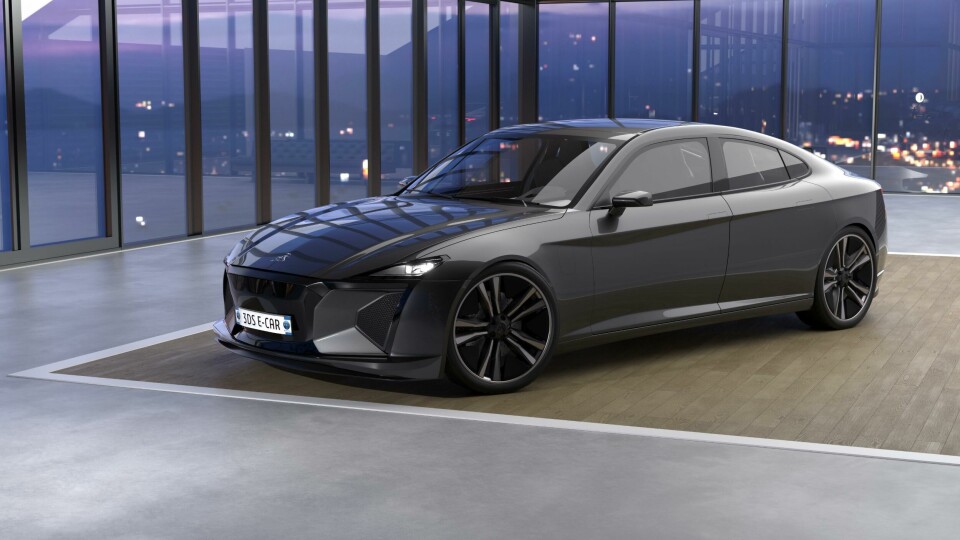
Digital platform brings designers and engineers together
With product design moving toward experience design and in-car experiences becoming increasingly digital, engineers and designers will need to work closer than ever. That has not always been possible, but advances in technology are helping to turn things around
Since its creation in 1981, Dassault Systèmes has emerged as a global leader in 3D software and now covers virtually all industries involved in design experience. Well established in the car design industry in particular, it has evolved beyond just software to become a complete platform. A core part of its offering is CATIA, a product lifecycle management system that is used to optimise workflow during product development.
Starting life in the late 1970s as a fairly primitive system, CATIA products have also grown to become something much bigger and more capable. Initially leveraged to model aeroplane wings digitally for the first time, it is now a sophisticated suite of solutions for all aspects of 3D product design and engineering. And to be clear: everyone has used a product at one point in their life that has been either partially or fully designed and produced with CATIA.
From products to experiences
Through “CATIA Creative Design” there is a complete range of solutions for Creative Designers, Surface Refinement and Visualisation experts available on the 3DPXERIENCE platform. These solutions help to manage the key challenges involved in both product and experience design.
With a paradigm shift leading to an increased focus on UX, consumers now expect impactful consumer experiences and not just “products.” Cars are also becoming increasingly connected and software-driven, but that experience must remain user friendly.
At the same time, heterogeneous and complex digital IT architectures struggle to connect creatives and engineers in real time – which is perhaps one of the biggest limiting factors for OEMs and suppliers to bring innovation to market rapidly.
Creative designers have access to all the necessary tools to cover the full design workflow
And although “Design Thinking” may be the dominant methodology for industrial designers today, its development stages have not adjusted to modern digital workflows and processes. Digital twins are also now mandatory to simulate and validate complex experiences and will be key in the move from Product to Experience Design.
So, how can 3DPXERIENCE help to manage all this? At a basic level, the platform provides solutions for designing, simulating, manufacturing and marketing products and consumer experiences based on a single source of information. It provides simultaneous access to real-time production data and assets for all project stakeholders, reducing error rates and speeding up the design process. And by gathering all players on a common digital platform, creatives can approach design in a far more holistic fashion, breaking the traditional silos between disciplines.
As for the CATIA offering, creative designers have access to all the necessary tools to cover the full design workflow: from the use of VR in human and product experience design to 3D sketching and Class-A surface modelling.
A common benefit to all visualisation and product experience solutions in CATIA is that there is no need for data prep as applications consume 3DPXERIENCE production data directly. Dassault Systèmes also offers life cycle assessment (LCA) functionality, providing the digital continuity that can help to realise a sustainable future.
The future
Creatives must become designers of a “system of systems” to master the complex interaction of hardware and software. A deeper collaboration between creatives and engineers of different disciplines is key. For example, physical switchgear in the car is being replaced by touchscreens and voice recognition, meaning UX designers must collaborate with software and systems engineers.
With CATIA’s common data model, iteration loops between disciplines do not suffer from the usual pitfalls around data exchange or out-of-date model data. With better accuracy and more iterations possible in a shorter amount of time, there is less of a need for physical prototypes in future – meaning substantial savings could be made. All in all, this is a gamechanger.