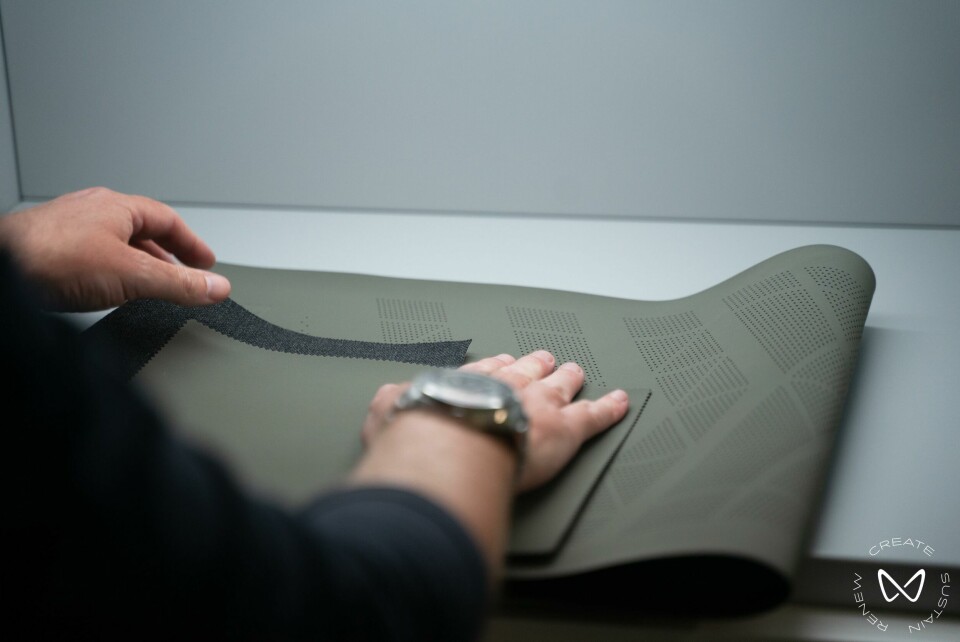
Innovation in CMF – new materials, challenges and changes
Carmakers and suppliers handpick a variety of new materials that could be used for interior design, discussing both the benefits and challenges of adoption
From cork to cactus, designers are constantly trialling new materials for use inside vehicle cabins. Alongside our CMF survey, Car Design News decided to find out which materials are currently showing the greatest signs of promise, and what challenges they may be posing as designers consider them for production models. And if the uptake of these new materials changes the way designers are working, might they also potentially have a far wider impact on the operation of the entire automotive industry?
Which new materials are showing promise in automotive design?
“A big chunk of new material innovation study is now related to sustainability,” Kyeong-Hee Shim, head of CMF at Tata Motors, tells CDN. “This could be using recycled materials, waste materials, or making sure the material is renewable at source. There are a few great initiatives for both soft and hard materials, and some of them have already been used in production vehicles.”
A prime example is Neoluxe – a knit suede developed by soft-material specialist Shawmut. The suede is made from 70% or 100% recycled content, transforming post-consumer or post-industrial waste into high-quality fibres. It can be used to clad almost anything inside the cabin, from seats to doors, pillars to visors.
Mollie Engel, vice president of design and development at Shawmut, helped to develop the material. “I have trimmed and manipulated it with everything from laser etching to printing,” she recalls. “It takes any embellishment beautifully, and it also moulds well. It is a very versatile material that significantly reduces environmental impact by minimising waste and conserving resources.”

As well as sustainably-sourced materials, Tata’s Shim is also intrigued by self-healing materials and coatings which have the ability to repair small instances of damage and thereby extend the life cycle. An example could be a polymer infused with microcapsules containing a healing agent. When the polymer is damaged, the microcapsules break open and release the agent, which then flows into the damaged area and hardens.
David Hopwood, CMF design chief of Mahindra Advanced Design Europe (MADE), also believes that self-healing materials could be a potential new area of exploration for interior design teams, alongside nano-bionics, advanced woven textiles and bio-based materials. These are all promising new solutions that could see greater uptake inside the cabin as development progresses and design teams continue to innovate.
“We are exploring every possibility,” he emphasises, “and are constantly pushing the boundaries of new materials, benchmarking across all industries and staying open to innovations that could enhance our customer story.”
Speed, cost, feasibility: the primary challenges of introducing a new material
Developing new materials involves countless hours of discussions, meetings, and even longer testing phases. Hopwood explains that it requires patience and a long-term mindset, as well as an imagination and clear vision for the potential uses of the material. He believes that a “materials-led design approach” is extremely important, whereby the material is carefully considered at each and every stage of the design process.
And it isn’t just the aesthetic appeal of the material or its functionality inside the cabin that must be considered. Hopwood emphasises the need for a clear business case when introducing a new material, ensuring that there is a cost benefit for the carmaker, or that it helps them meet a sustainability goal.
This all takes a great deal of time, and according to Jorge Diaz-Martinez, Dacia’s chief colour and materials designer, managing that time effectively is a big challenge. He refers to the fact that companies around the world, particularly those in China, are continuously reducing vehicle development times, and as such, CMF teams need to work faster and more efficiently, even when the introduction of a new material requires extensive testing and preparation.
Regardless of the innovation, the material will not make the cut unless there is a tangible added value
“Sometimes, samples jump off the table. They shine with their uniqueness, and in C&T design, it is our job to see the opportunities that this can bring,” says Diaz-Martinez. “What is challenging, but also very exciting, is starting with the blank page that a new material represents. Specifications are not set in stone, so it becomes a true team challenge to bring it to life – not only in design but also through close collaboration with our lab and engineering colleagues.”
Shim highlights a similar point, suggesting that new materials could show signs of promise but may also be far from meeting the high specification standards required in the automotive market. If the material shows enough potential, materials engineers can be deployed to bring it up to required specification, but this “can take years and is often very costly.”
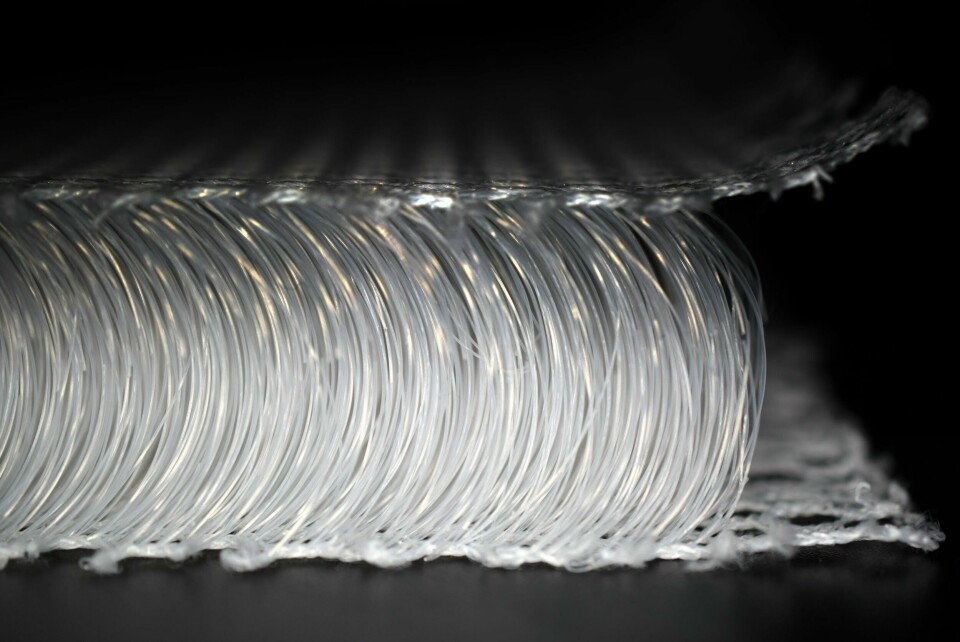
Once a material has reached required specification, the process of project implementation begins. Shim suggests that this typically involves numerous iterations of design development and refinement, once again eating into time and R&D resources. This needs to be checked from a cost feasibility perspective too.
“At the end of day, regardless of the innovation, the material will not make the cut unless there is a tangible added value,” Shim emphasises, echoing Hopwood’s earlier sentiments. “Challenges are coming from many angles. Time is one challenge, cost is another, and neither can be ignored. Story creation becomes important here so that we can persuade the business to commit the time and cost required.”
Could innovative materials reshape the industry as a whole?
“This is totally possible,” Shim remarks. She thinks that, with the increasing use of recycled materials inside the cabin, circularity and ‘closing the material loop’ may change the way that the automotive industry operates. Design and manufacturing will need to consider material circularity, ensuring that each component is produced with the foresight of disassembly at the end of its life. This could ignite growth in the use of mono-material structures, making it easier to recycle and disassemble.
A good example of this, she says, is the ‘Futurecraft Loop’ by Adidas. The shoe is produced using a single type of plastic, which at end of life, can be sent back to the factory, deconstructed and made into a new pair. However, the single material is currently 100% virgin plastic, as Adidas needed to ensure that it is completely pure in order to close the loop. Therefore, it may eventually have a positive long-term impact on the industry, but potentially at the cost of an initial spike in environmental footprint.
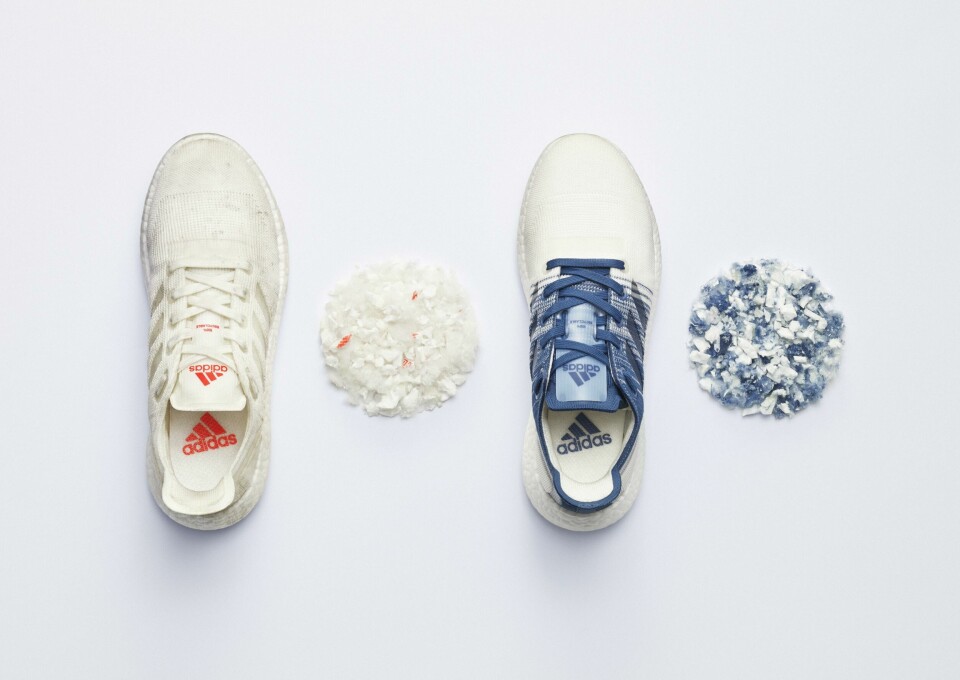
Both Hopwood and Engel expect the relationship between carmakers and suppliers to evolve as new materials are introduced into the cabin, with a more collaborative approach to the supply chain and the design process. This could help both parties react quicker to market demands, and could ultimately streamline the development of new vehicles. Engel also suggests that the adoption of new materials will likely require many different manufacturing techniques, with specialised weaving and bonding processes needed for the next generation of textiles, for example.
But perhaps the most intriguing change will be at a consumer experience level, she continues. Drivers and vehicle occupants have been subject to decades of experience with familiar materials like leather, plastic, and chrome. Replacing these with more sustainable alternatives, for example, could require a dramatic shift in mindset. But Engel is confident that many of the new materials that are being developed offer an equal, if not much improved, customer experience.
“Additionally, integrating technology into these materials, such as using materials for light and sound transmission instead of plastic housings, will enhance the design and the driving experience,” she adds. “Overall, the introduction of innovative materials in automotive textiles can catalyse a holistic transformation, impacting not only design and production but also the entire lifecycle of vehicles, from manufacturing to end-of-life recyclability.”