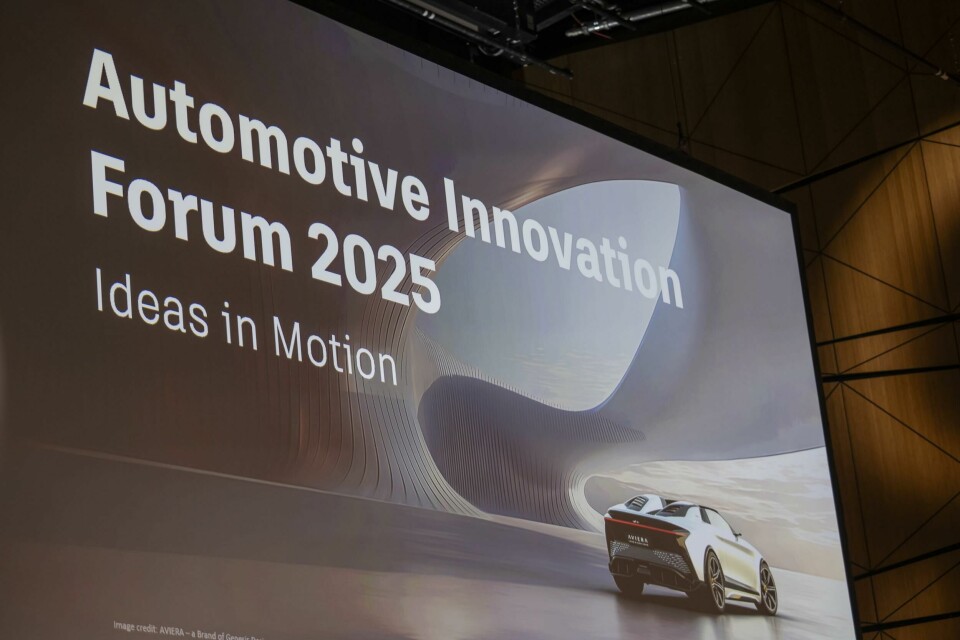
Review: Autodesk Innovation Forum 2025
Warm weather and hot topics combined well in Darmstadt as Autodesk experts and customers shared current future opportunities for the software
Now running for a decade, the Automotive Innovation Forum (AIF) brings together a huge range of experts from a wide mix of industries. One thing in common – aside from an unhealthy appetite for networking – is that all of these experts use Autodesk products in some way. The idea is to share ideas, success stories and address shared challenges all under one roof.
The conference is split into two main tracks: design and smart factories. Design remains the core focus for most visitors over the two-day show, and sessions tapped into both broader, more abstract themes alongside deeper case studies.
It is only the second year the AIF has been held in Darmstadt, not far from Frankfurt, but for some attendees it was very familiar territory. Having grown up and studied there, Autodesk’s Jörg Winzenhöller affirmed in his opening keynote that “Darmstadt is the place to be.”
Adaptability
The programme this year was built around the theme of adaptability, and this was evident throughout. In fact, the morning included an inspiring slot with Raphael Gielgen, a “trend scout” for furniture brand Vitra. As an outsider to automotive, he observed that “form may not follow function” and instead “follows the future… and never before has the future become the present so fast.”
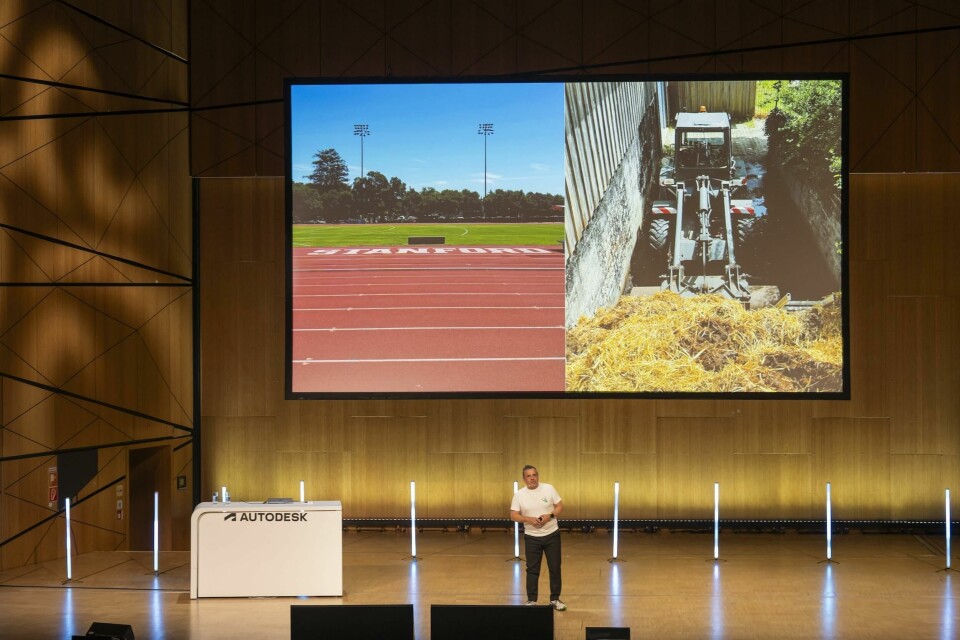
Indeed, speed was another central theme. This urgency to get products out is pushing designers to work in different ways, and Gielgen does envision a roll-out of more lifelike metaverse-style workspaces as a result. A little bleak at times – championing AI as far more than an assistant and in fact a worker with an open contract – he did bring things back to the physical realm with a discussion around the duty of design. “This is to bring beauty back into the world,” he emphasised, adding that human storytelling is key. “Our strongest tool for the future is our voice, our narrative.”
All this dug into wider themes around uncertainty and humans’ natural resistance to change. What does this mean for design? Well, how new tools are adopted for a start, plus how new technologies are integrated in the car itself and even how styling trends might evolve. For example, resistance to change could prompt homogeneity or bland design. If change is embraced, perhaps new typologies or themes are explored. Change is not inherently good, of course, but it is when categorised as progress. This is what the industry should be seeking, not change for the sake of creating ‘newness’.
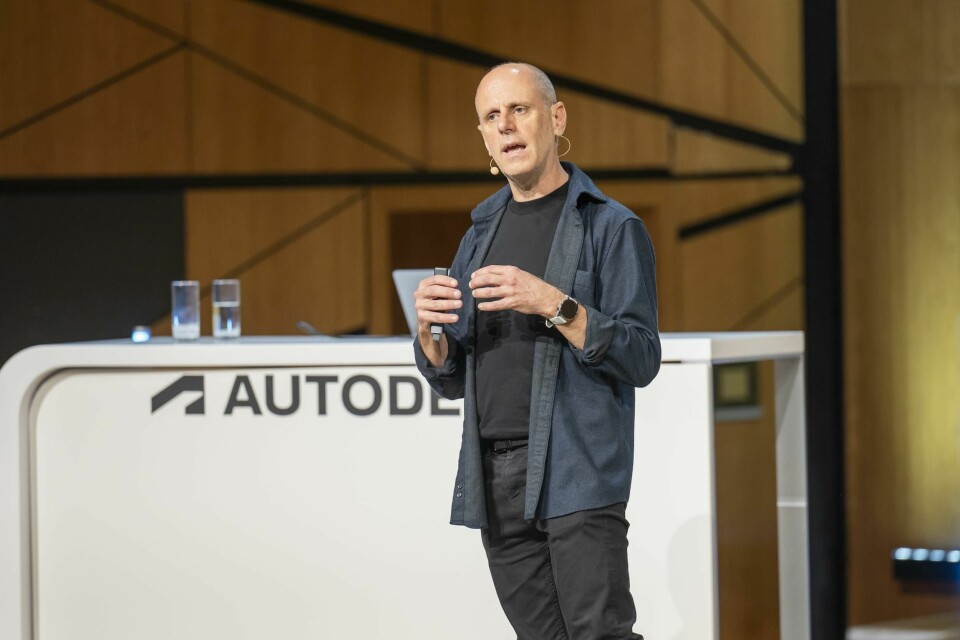
Futurist Mike Haley tied similar themes into his discussion about Autodesk’s own trend forecasting. Under the guise of “shape, perform and make” he suggested that AI is already fundamentally changing how designers address problems in their day-to-day work. For example, Project Bernini showed how Generative AI can create 3D models from 2D sketches in a matter of seconds; not entirely unique, but we are sure the programme has progressed beyond what could be shown on stage.
Elsewhere in the Autodesk sphere, Navasto can quickly show designers how aerodynamic their car is through AI-supported simulation. “Sim is what gives life to your design and gives you information early on in the process,” noted Haley. “It changes the way you do design.” Like Gielgen, Haley also pointed to a resurgence of “beauty” alongside the spike in AI. “I think we’re going to start making beautiful things again, and bringing beauty to efficiency.”
Parked out front was a curious-looking hatchback, a new electric city car designed by Nio off-shoot Firefly. Sold under the same name, this model framed the basis for a discussion around reinventing HMI, in particular, but also simplifying exterior design somewhat. All this was enabled, of course, through today’s digital tools. Like many other projects shown during the day, VR played a key role here too.
Designers Mansour, Guillaume and Philipp manned the stage, with a virtual cameo from Kris Tomasson too. We enjoyed the focus on “purity,” evident in the circular head lamps (we went for the most pure shape, which is the circle) but also a digital detox. “The form language is very clean, an antidote to chaos we see on European roads,” said Mansour. “We don’t want people fiddling around trying to find buttons [either].”
Immediately after came a duo of digital modellers from Nio proper, who explained how they had built their own solution to streamline the development process. Christian Falkenhagen (above) recalled handing over a project for sign off and reflecting that the entire process of creating those images and digital models had been a bit of a… pain. An interesting session, and remember that expression “build your own” as it is relevant later on in this article.
Tools should be scalable, secure, user friendly and collaborative
Presenting for Hyundai, Chayeong Kim gave immediate kudos to her colleague Youngbok You who “is the person who can actually answer all of your questions later on.” Clearly very modest, Kim proceeded to hammer home a polished presentation that addressed how initial concepts and proposals often don’t look as they should when returning from feasibility checks.
For example, rather than shrugging and accepting that an initial design will not meet certain regulations, the team should ask: is there a better way? Do we have to accept this? The solution, in simple terms, is to employ software that allows designers to check different elements themselves along the way, rather than waiting until the end.
One example showed how a complex grille design could be made to comply with certain regulations around bumper protrusion, using a tool that can suggest tweaks to certain geometries. The result is that the original design intent is largely unchanged and it can proceed to production safely.
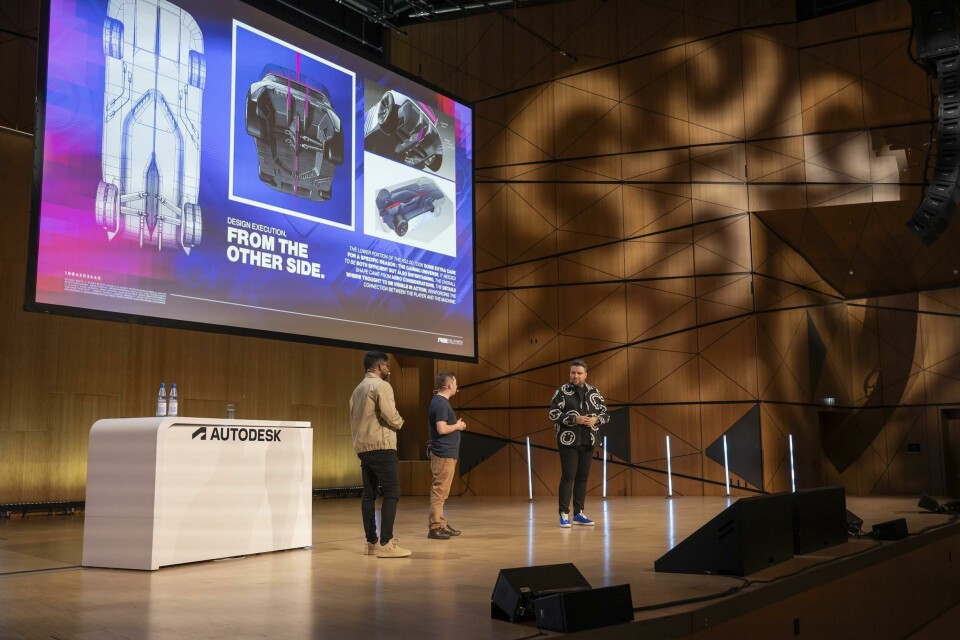
At Ford, the design team from the Cologne studio took to the stage to recount a secret project that went ahead to celebrate the 40th anniversary of the RS200. We covered this on CDN last year following an exclusive invite (just saying) but this time round the trio of designers Michael Barthley, Karthick Pamisetty and Lukasz Wojkowski went into more granular detail on the kind of tools that were used. The underlying takeaway was that due to the nature of hte project, things had to get done quickly, often away from the office and ultimately to a quality that meant their boss was okay with them moonlighting on something away from their ‘day’ job.
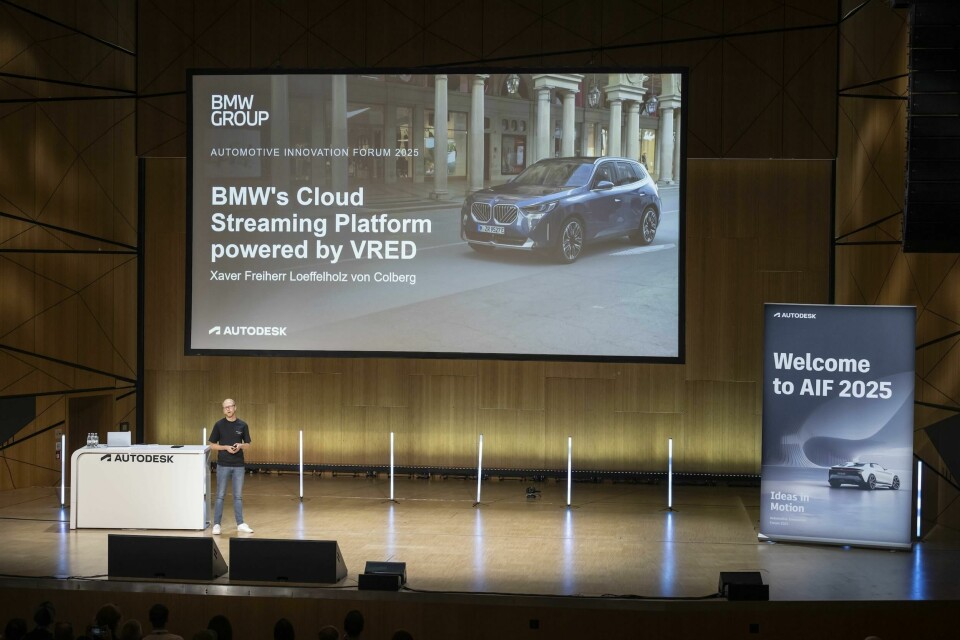
Alongside the overall theme of adaptability was the idea of connectivity. Not in the Bluetooth sense, but human-to-human. Autodesk’s Winzenholler spoke of the desire to “build connected design workflows around the globe” and various presentations across both days illustrated how this is being done. BMW’s Xaver Freiherr Loeffelholz von Colberg championed an unlikely candidate – public cloud platforms – but explained that “tools should be scalable, secure, user friendly and collaborative… Cloud set-ups are useful for this.”
It is is paramount to understand that this is not a miracle or a magic trick, it’s real
Specifically, BMW has built a means of transforming a series of images into an interactive 3D model which can be viewed easily by various members of the organisation. The suggestion was that designers from different parts of the world could easily gather and work things out without having to go through a more complex visualisation programme, and hinted at the ability to fast-track design sign-off by getting Top Brass “into the room” hassle free. “Using the VRED Core app you can control a larger display though your phone too, using it as a controller that is easily accessible and convenient with no special VIS hardware.”
Colberg also flagged a recent AI project through DepixAI, using image generation prompts to place vehicles in different landscapes or lighting conditions with ease. “It’s nice for marketing shots or if you just want to see how it looks in different environments,” he continued. “You can really play around; I started using dragons in mine, but wasn’t allowed to use this in official marketing… I’m not sure why!”
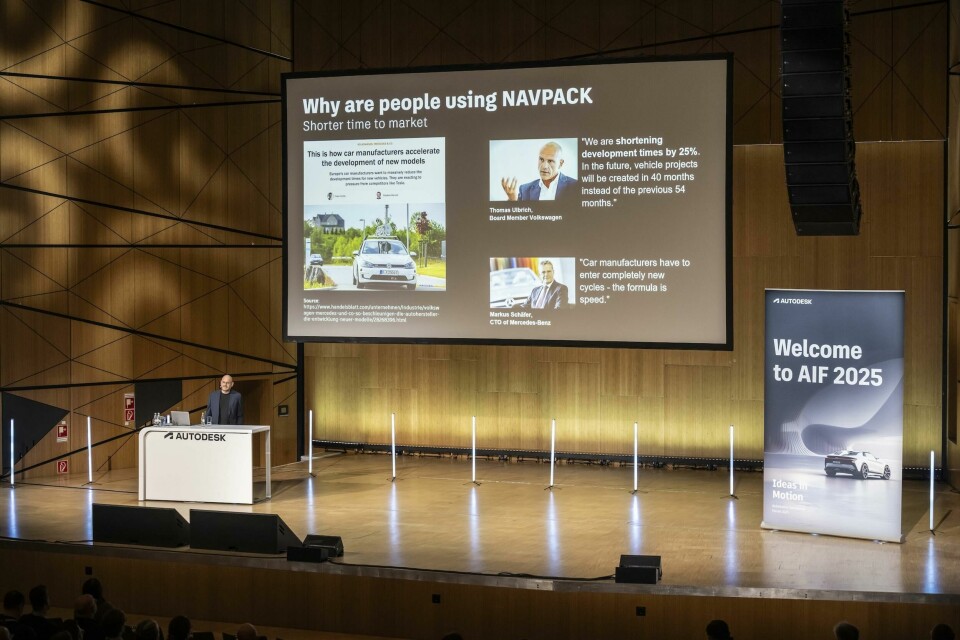
Matthias Bauer then shared some insight into how Navasto (now an Autodesk product since its acquisition) is supporting AI-informed design. Mike Haley had already flagged a couple of instances (earlier in this article) but in this case Bauer focussed on how generative AI could be used for geometry refinement and optimisation. “During design you have something on your screen but you don’t know how it performs, and may need to be sent to engineering. This can be sped up with AI,” he says.
For example in CFD simulation or for crash test predicitions, taking seconds versus hours and rendering almost indistinguishable results. “It is is paramount to understand that thits is not a miracle or a magic trick, it’s real. But at the same time, it is not a complete substitute.” Bauer classifies it as the integration of physics-based information into the process of design.
Believe it or not, this too touches on the idea of beauty and aesthetics in car design. By training the AI with customer-specific data, the model can take into consideration the design language or intended themes of a particular brand or model set. This means that it can recommend new geometries that are aero-efficient but also in line with brand style. “If everyone designed the optimum aero shape, you will end up with a droplet. And nobody wants that.”
For Xiaomi’s digital design director Xue Jun, part of the company’s ability to accelerate its entry into the automotive space was approaching design in a new way. He believes there is a transitional challenge as design progresses to the modelling phase.
“Drawing is easy, modelling is hard,” he mused. “But digital design is not just about well-executed modelling. It starts from the ground up, we need to stop thinking like specialists and start thinking like users.” He describes the change in dynamic as “hitting like a tonne of bricks” once he realised the potential of simply “acting fast and executing.”
All of this is a little buzzwordy, but his point is relatively simple: be willing to adapt on the fly. While Xiaomi is not promoting knee-jerk reactions, the approach is to find new ways to optimise the design throughout even in the latter stages. “If we find that market needs change, why not follow? Don’t resist or worry about change; as long as we follow the needs, we are on the way to progress.”
Which tools are supporting this way of thinking? You guessed it. “AI can turn 2D lines into a full silhouette with multiple evolutions and colours in HQ renders. The same can be done for wheel design. It increases the number of possible prooposals and turns 2D into 3D renders quickly. You might have a small sacrifice in accuracy, but a huge increase in speed.”
For this year’s student competition almost 70 students entered across nine schools, the finalists making it over to Darmstadt and joining Thomas Heermann on stage to announce the winner. “It’s amazing to see all the talent and how they use our products to bring their ideas to life,” he noted. It was Coventry University that took the prize, with the University of Staffordshire and Politecnico di Milano runners up.
“We had a lot of fun,” said one Staffordshire student. “It was an opportunity to be really creative,” added a Coventry winner. One of his course leaders noted: “We’ve always had a good partnership scheme, especially with Autodesk, making sure we teach the right things. That support can really boost what the students are able to do.”
Richard Gilmartin, who leads the Staffordshire programme noted: “[The professionals] also enjoy seeing what the youth of today are coming up with today and it’s good for them to get inspired. Our two masters students worked with Kadence to help them develop, so it’s really important to have partnerships.”
While the prize and recognition (and night out in Darmstadt) is all well and good, perhaps the real plus is showing your skills to a crowd of potential employers or internships. As Autodesk’s Heermann pointed out: “They could be your next Alias modeller.”
This year’s AIF brought together a heady mix of topics and speakers, many of whom showed how AI is far from theoretical and now a very real – in some cases core – part of the development process. VR and AI were undoutedly the hottest acronyms of the day (as they were last year) and there is clearly a huge degree of innovation that has gone on. More is on the way.
It is also worth noting quiet concerns that large organisations are too slow to adapt and react to changes elsewhere in the industry. Smaller dedicated AI programmes are coming out of the woodwork, for example, affording designers freedom to play and at least try things out even at a basic level – and for free. Enterprise products remain the foundation for professional projects, but providers will need to take concerns like these very seriously, improve their agility and provide support when it is asked for. If they don’t, designers will use other solutions or simply build something in-house that works for them.
Watch out for more AIF content to come, as Car Design News sat down with various designers from the likes of Chery, Ford, Incari, Tata and Firefly during the course of the day. Plus to look back on past editions, here is the round-up from 2024 to see how topics may have progressed.