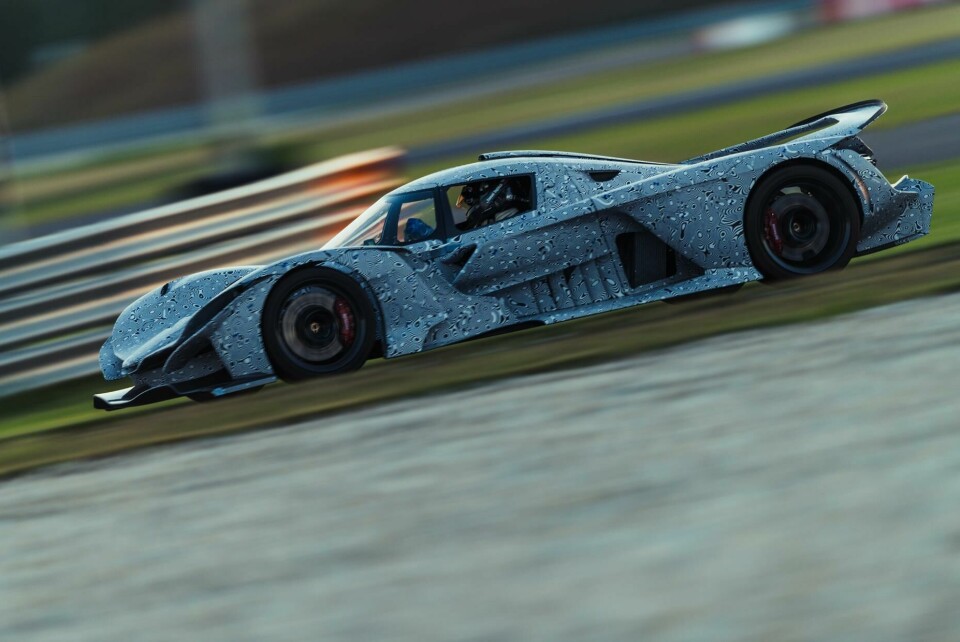
Praga design boss on the Bohema hypercar
Head of design at Praga Cars, Juraj Mitro, discusses the design process behind the Praga Bohema, the influence of engineering and aerodynamics, and the crossover between furniture and car design
Car Design News spoke with the head of design at Praga Cars, Juraj Mitro, about the design process behind the Praga Bohema, Praga’s first road legal hypercar. Mitro also runs furniture company Mitro Design with his wife Etela and focuses on using non-traditional materials such as carbon fibre and concrete.
Car Design News: What were your key priorities for the Bohema design?
Juraj Mitro: Plain and simple: functionality and emotion.
CDN: How did you approach creating a hypercar that stands out from everything else?
JM: The base concept came from the Praga R1 in 2011. Bohema is a completely new car but you can feel the common line. For me, it is one path of inspiration as well as learning, passion and an open mind. Honestly, we didn’t look at what anyone else was doing, we followed our own ideas.
CDN: What influence did aerodynamics have on the design?
JM: It has a huge influence on design, but we took it as a priority and a challenge. Bohema doesn’t pretend to be aerodynamic; the main part for aero downforce takes place under the car. We did hundreds of CFD simulations. During the development we tested the aerodynamics and downforce in the F1 wind tunnel with two different prototypes.
I don’t see a difference between design and engineering priorities in a project like this
CDN: What engineering considerations impacted the design?
JM: The base packaging is extremely tight. Because we decided on an open light visual concept, the bodywork is skinny and you can feel the mechanical parts underneath.
CDN: What are the key design considerations when designing a hypercar for the road?
JM: Maybe it’ll sound like a cliche, but the most important thing is to have a target. Our goal was to create a race car with a licence plate. We didn’t have a target for maximum horsepower, torque or top speed, our focus was purely on creating the fastest car on the race track and it’s a very complex task. Of course it couldn’t just be a purpose-built car. The design must also take into account the aesthetic, emotional requirements and message of Praga race cars.
CDN: What is unique to the design of the Bohema from any other hypercar?
JM: She is like the wind (CDN notes the Patrick Swayze reference).
CDN: How did road safety requirements impact the design of the Bohema?
JM: We took many ideas from motorsport, so the passive safety level is very high. The monocoque is extremely stiff and it’s got a big crumple zone supported by zylon panels on the side, front and rear crash boxes as well as a six-point harness inside. All safety considerations are a natural part of styling.
A deeper understanding of the technology opens the door to more freedom in styling
CDN: How does the design process differ from Motorsport design?
JM: Motorsport design should be 100% functional. The rules are a barrier but I don’t agree in that context that livery is the only job for designers. For example, the design story of the Praga R1 race car was the story of sculpture. That was a creative process of shaping the aerodynamics and the ergonomics in accordance with rules.
CDN: What drove the decision to use carbon fibre? Was it design led or engineering?
JM: I don’t see a difference between design and engineering priorities in a project like this. We have a lot of experience with carbon fibre. A deeper understanding of the technology opens the door to more freedom in styling. Bohema’s target was to be under 1000 kilograms and there is only one way to achieve that, by using highly sophisticated carbon composites.
CDN: What are the advantages and disadvantages of working with carbon fibre?
JM: Each composite part is made by autoclave. It is the best way to create these panels, however it’s the most expensive way. It’s also the right choice for low volume production. It’s a relatively flexible process, open to parts alterations during the production period, but it’s sensitive to human factors in the production process.
CDN: Were there any other design concepts considered before the final design was signed off?
JM: Just one concept. We were sure what the target was and discussed this a lot during the process with everyone involved in the project. Naturally, there will always be designs that don’t progress to the final product.
CDN: Walk us through the interior design process, what decisions were made and why?
JM: At first we did an ergo mockup. The focus was to create a cabin as narrow as possible for two people because of the aero efficiency and proportion of the whole car. We tested a lot of alterations, it took years and a lot of clay work! We were trying to make the package as tight as possible. The reason was to keep the weight low, with torsional rigidity, high stiffness and aero balance. Everything had to fit perfectly to meet the aero-light styling.
CDN: Who or what is your design inspiration?
JM: The team spirit is the best inspiration. Everyone involved in the project could point to a process and become a designer and any well-engineered details can inspire.
CDN: What are the similarities between car and furniture design?
JM: For me it is the same kind of work: understanding the material. The carbon fibre is not just a visible structure. It gives me freedom in shape. It’s about pushing the emotion and engineering on the visual and physical limits. It is about creating artefacts.
All images by Matúš Rendek