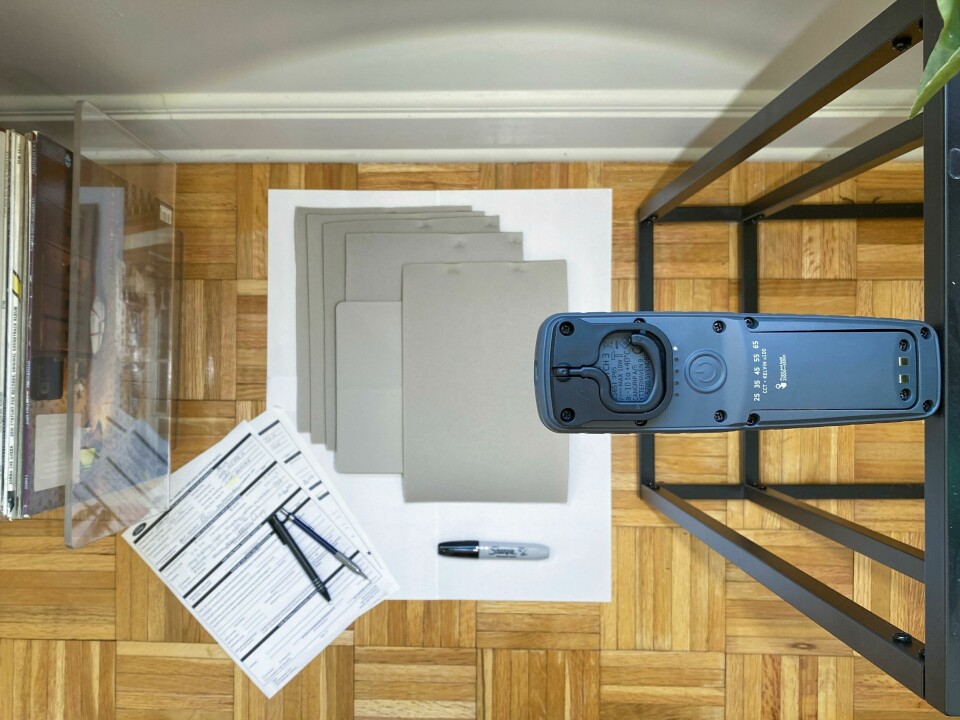
How to do car design remotely – Ford colour and materials
The Coronavirus pandemic has changed the way in which millions of people around the world are living and working. The automotive industry is scrambling to adapt, and while some areas such as manufacturing have come to a halt, the latest digital tools are allowing car designers to keep going.
In this series of short articles, Car Design News talks to the world’s leading designers about virtual car design, the challenges and the possibilities.
Ford’s colour and materials design manager, Allen Brown, describes how he and his team have adapted the way they work.
How to do car design remotely – Hyundai and Genesis
If there is one area of car design that involves humans coming into close contact with each other its definitely colour and materials. We literally gather around samples to look at them, touch them, and then discuss them.
I am in charge of the mastering designers. It’s on us to work with the suppliers to take the materials and develop them in the right colours. The vehicle designers along with the colour and materials team propose the outfits for each vehicle, and then they come to us with the plan. We then work with the suppliers to get the right materials.
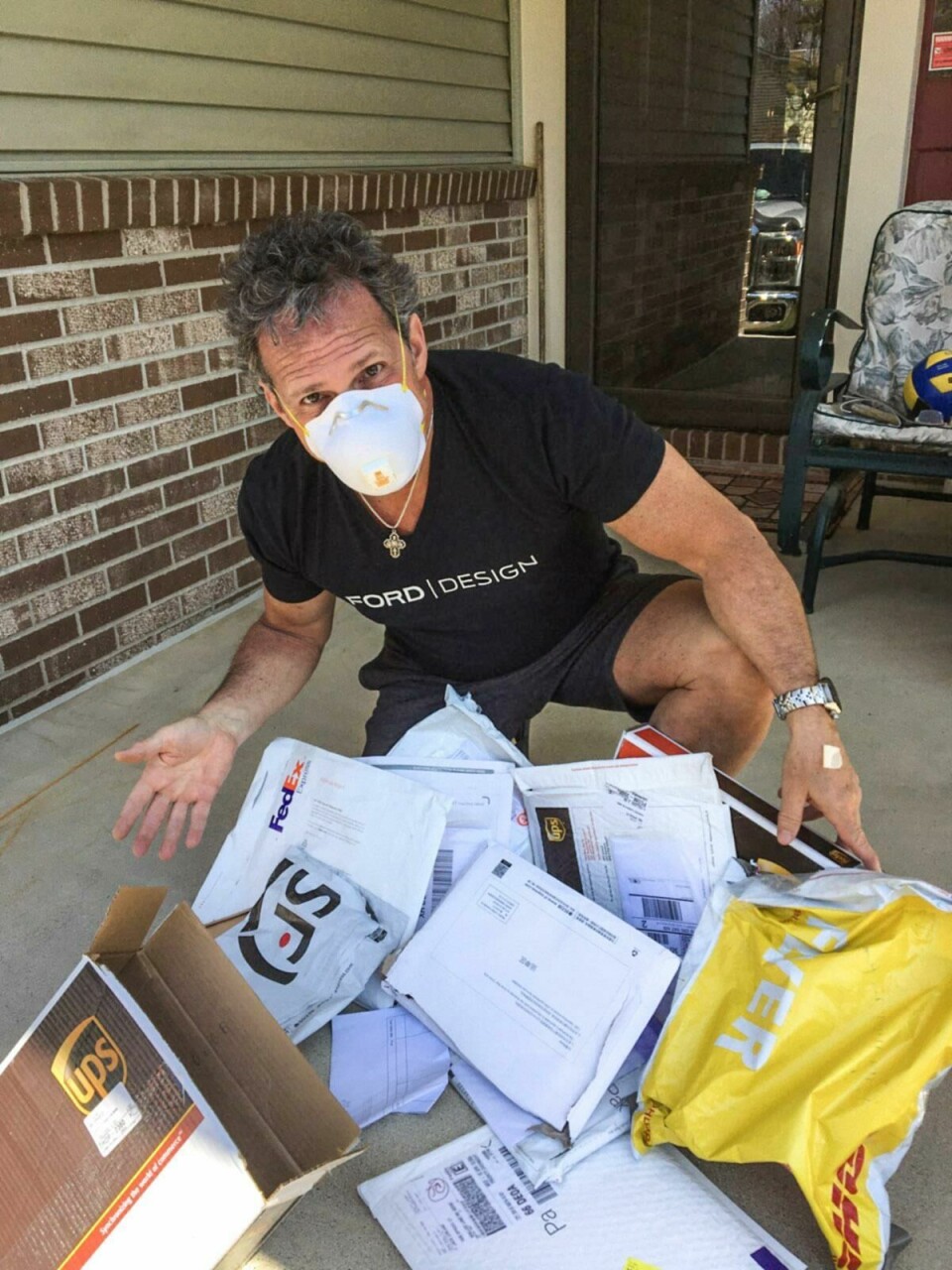
If you think of all the materials that go into a car, it’s a herculean effort. We start with a colour target, and then we work to make sure that the thread matches the leather, and that those both match the fabric, and that it all matches the webbing.
To do this, we work with suppliers every day and look at the colours of each material under specialised lights. And because materials have so many different chemical make-ups, they have to be coloured in different ways, which means there is a high propensity for metamerism. This is when the colour of two materials looks the same in one light source but looks different in another light source. Have you ever put a pair of pants and socks on in your room thinking they match but then walked outside and realised the pants are black and the socks are brown? They are metameric to each other. And that’s what we are trying to avoid.
So the lights we use mimic three conditions: bright sunlight outside, daylight in horizon, and also a showroom on a cloudy day with cool white fluorescent. We check all the materials under these settings to make sure the colours of the materials are accurate. If they are wrong, we tell the supplier and they come back to us with another sample.
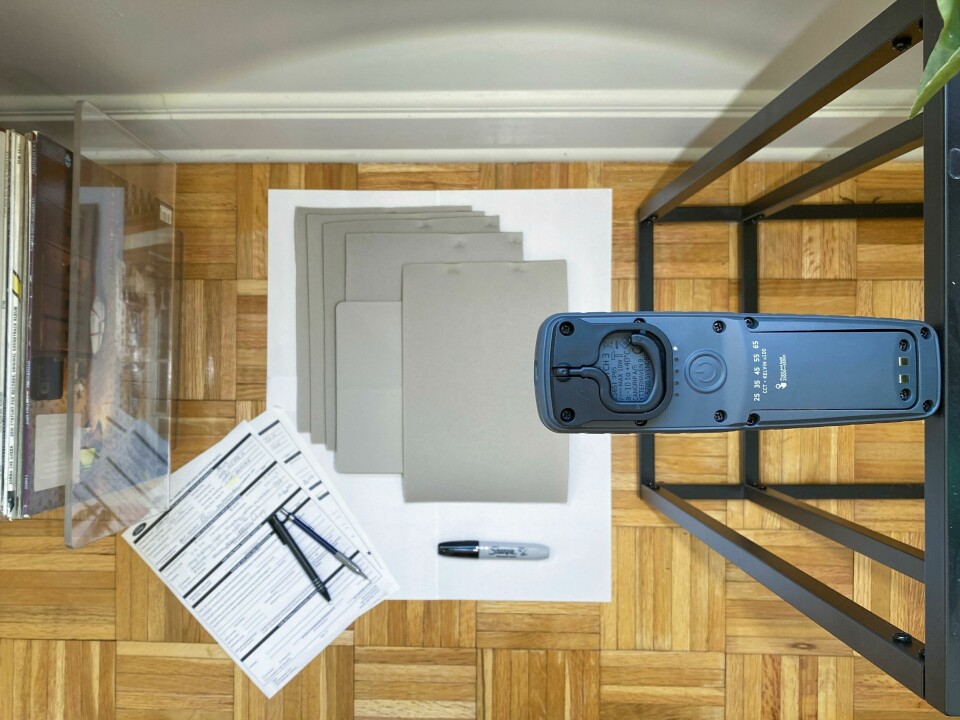
We couldn’t use this workflow during the pandemic, so we’ve been trying out some new handheld scan grip lights to use at home, and they have been working really well. They replace the giant booths that we would normally drag a part into in the studio. Six people in my team, including myself, are using these at home. Our suppliers are shipping the materials to us so we can look at the them, provide comments as usual, and send them back with the completed paperwork.
The first couple of weeks were a little rocky. But then our suppliers were relieved as we were still able to work together despite their factories being closed. It took a couple of weeks to get over the hump and then we got into a groove. It’s been very positive.
There is a nuance of being together standing over a material in the studio. It really allows you to bounce ideas and thoughts off of each other. We’re doing this digitally right now, but it’s not quite the same. But for the most part it has been working very well.
We’ve got projects going on right now where we are correlating the digital with the physical. We have highly calibrated monitors that allow us to view materials, but we are still using the lights and the physical materials too. These digital tools have come a long way, and it’s now moving towards virtual reality where we can have a library of materials that we can gather around and look at in the virtual space.
But we aren’t quite there yet – we might use the digital tools to narrow down our selection and choose a few contenders, but we will then use physical samples to select the final one. When we are designing something we also need to think about the haptic experience, and we can’t really do that yet with digital tools.