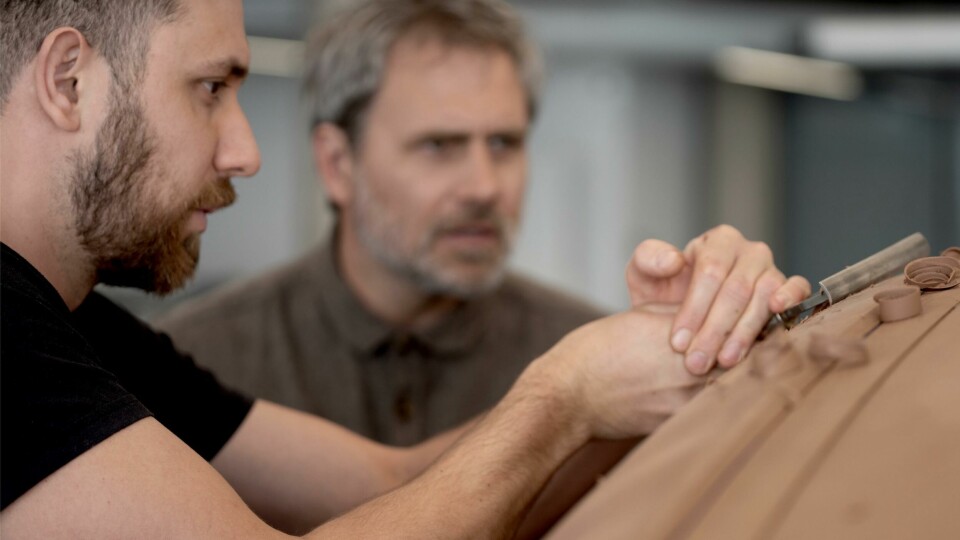
New Model Army: inside Tata Motors’ clay studio
With a brace of wins at the CDN People Awards, Tata Motors has an enviable reputation for having one of the best clay modelling teams in the industry. Car Design News paid the team a visit in their state-of-the-art facilities in Warwick
“I always say that you will struggle to nominate a working-level function within an automotive business that impacts its success more than physical modelling,” says Tata Motors’ senior clay modeller, Mark Welland. “The most important decisions are made around the properties that we produce.” Stood on the shop floor of the clay studio with a full-size property a few feet away, it is hard to argue to the contrary.
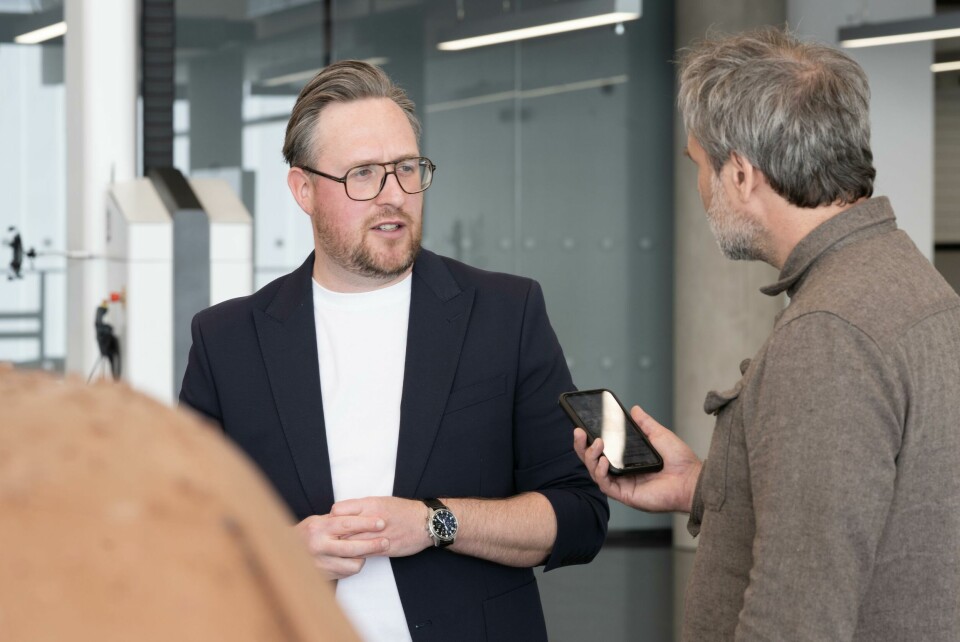
Yes, digital design tools are becoming ever more sophisticated, which has affected the role of traditional methods, but there is an emotive power rendered by clay that cannot be denied. When time is short, a well-resolved model can communicate an idea with a clarity and speed that is tough to beat. That is clearly Welland’s belief – he leads a team of 11 modellers with a broad range of skills. Tata’s global design director Martin Uhlarik is a believer too, overseeing substantial investment in state-of-the art milling machines that complement and enhance the hands-on activities of the team.
“Designers will know what they want to do, but you have to have a feel for how they can maintain their theme while covering all the hard points”
Welland’s team is good. At the end of last year, Tata triumphed in the CDN People Awards, claiming the best modelling team in the teeth of stiff opposition from Volvo, fellow Indian brand Mahindra, Changan and next door neighbours on the Warwick University campus, JLR. That luxury brand looms large in Welland’s orbit: the modeller learnt his trade there, joining as an apprentice in 1999, inspired by an encounter in his formative years with a model of the XJ220. “I think I was about 12. That was a light bulb moment for me.”
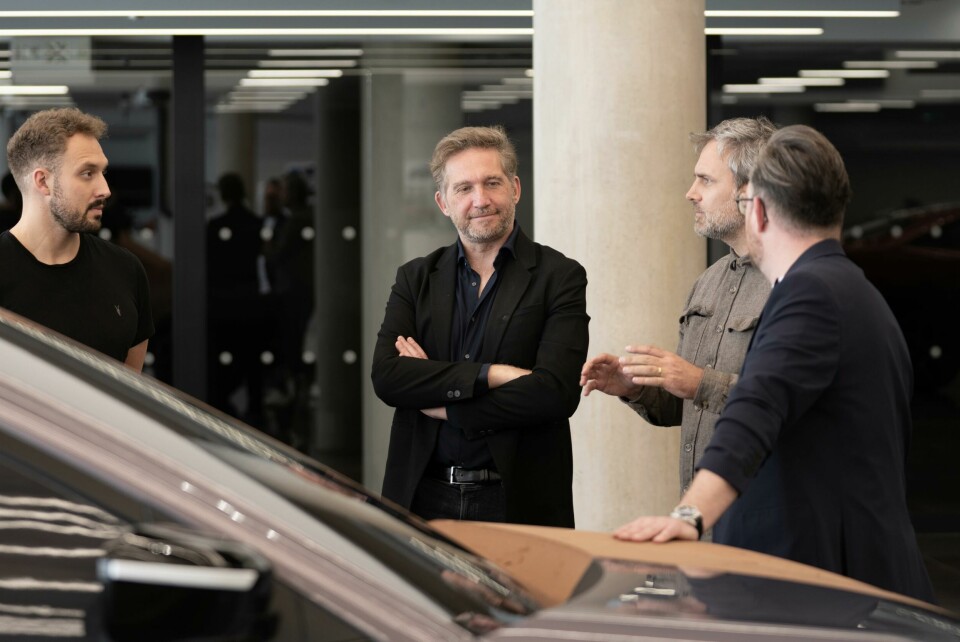
By his own admission, Welland was not a natural draughtsman but had good spatial awareness and an aptitude for problem solving. As any modeller (or designer for that matter) worth their salt will tell you, problem solving is essential. “Designers will know what they want to do, but you need to have a feel for how they can maintain their theme while covering all the hard points – door handles are a good example,” says Welland.
When Welland joined Tata in 2016, it was a bare bones operation producing small, low-cost cars for the Indian market. As the OEM’s ambitions grew in lockstep with the nascent middle class aspirations of the country, the team also grew, with the new clay studio head recruiting former colleagues that would fit into the dynamic. Currently, the headcount is 11, all people Welland had experience of working with. Like good tradesmen working on a site, there is a healthy amount of banter alongside a respect for each other’s abilities.
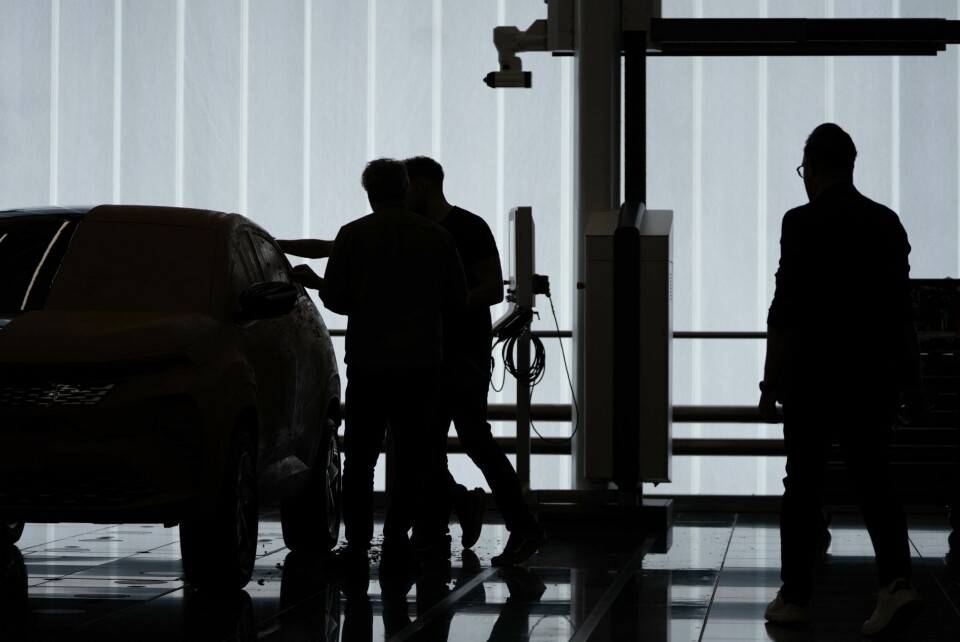
“Exterior modelling is hard work, crashing into a bodyside burns a lot of calories. Interiors are more about refinement and detail.” Testament to the former are two of the team who look like they would be first picks in a tug-of-war team. “Yeah, they can shift some clay,” Welland confirms. Tools of the trade differ, according to the task at hand, but there are some pleasing moments of improvisation too.
Cross-functional collaboration is ever more important. As Welland points out, the days of four- or five-year product development plans and competing parallel design themes went the way of the dodo. These days development phases top out at two years, with 18 months seen as the optimum. Like the proverbial snowball at the top of a hill, the process will only get faster with ever more input contributing to processes that are both complex and speedy.
“My advice to aspiring modellers would be to seek out experience at a trusted first tier suppliers”
“There is a ‘get the theme right first time’ culture across the industry now,” says Welland. This means the team must move with the same alacrity as the design and engineering departments that rely on them. “If engineering propose feasibility-related changes, we need to feed that into the physical model quickly to enable the creative teams to react,” he continues. “We are scanning and milling the clay models almost weekly. Those scans will either feed into the digital modelling and visualisation teams or be offered to the studio engineering teams for feedback on feasibility. Then the studio CNC machines can mill in a fresh hardpoint zone or some data that the designer feels is currently further refined in the CAS model.”
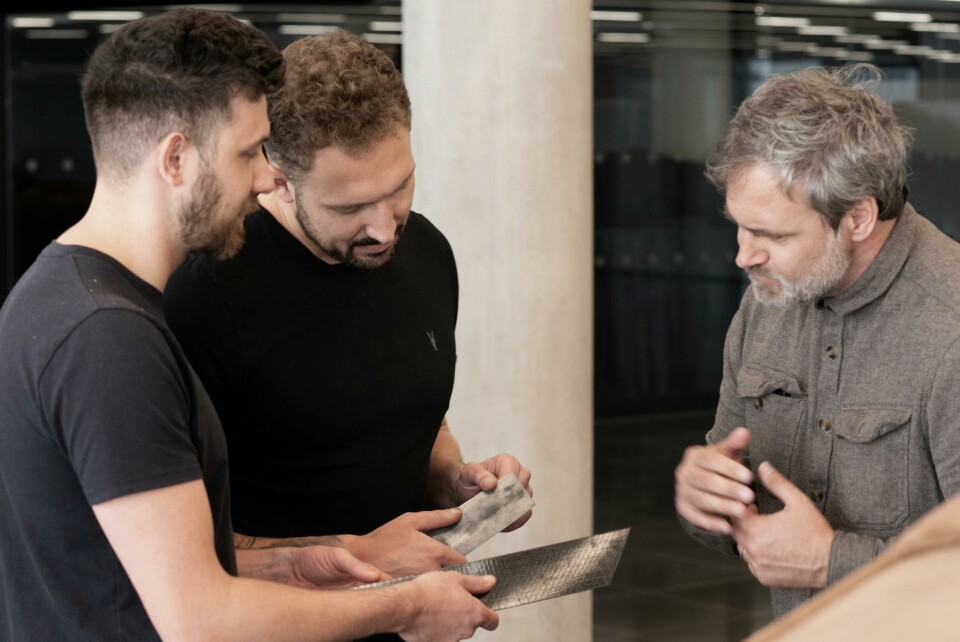
“Clay is the best way to quantify and refine the design,” adds Uhlarik. “If you’re doing a production program, you have to just recut and recut. The more times you loop the design in clay, the better it gets. It’s like a samurai sword. You fold it a thousand times and it’ll be unbreakable.”
Uhlarik is a clay advocate, but what about the future of the discipline? Welland is bullish about the short term prospects but sounds a note of caution when casting his eye towards the horizon. “As an industry, we are doing very little to nurture an ageing skill base. Apprenticeships or academies within the big OEMs are a rare sight,” he says. “My advice to aspiring modellers would be to seek out experience at trusted first tier suppliers.
“They are often willing to give keen grads or juniors a chance. Although sometimes a little more chaotic than an OEM experience, you will get exposed to the same processes and pressures of an internal design studio. Who knows, you might just catch the eye of one of the supplier’s key clients.”
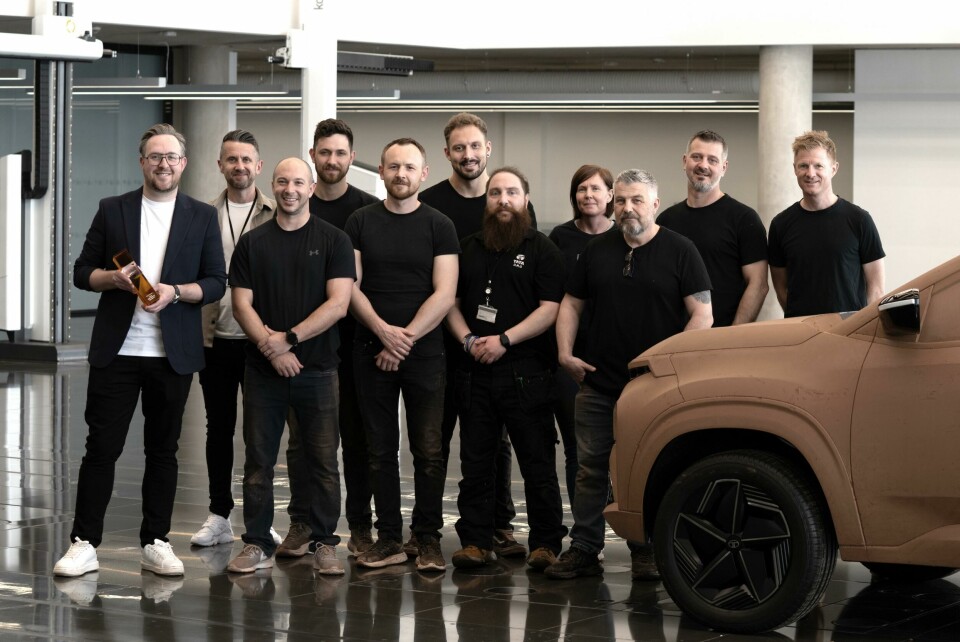