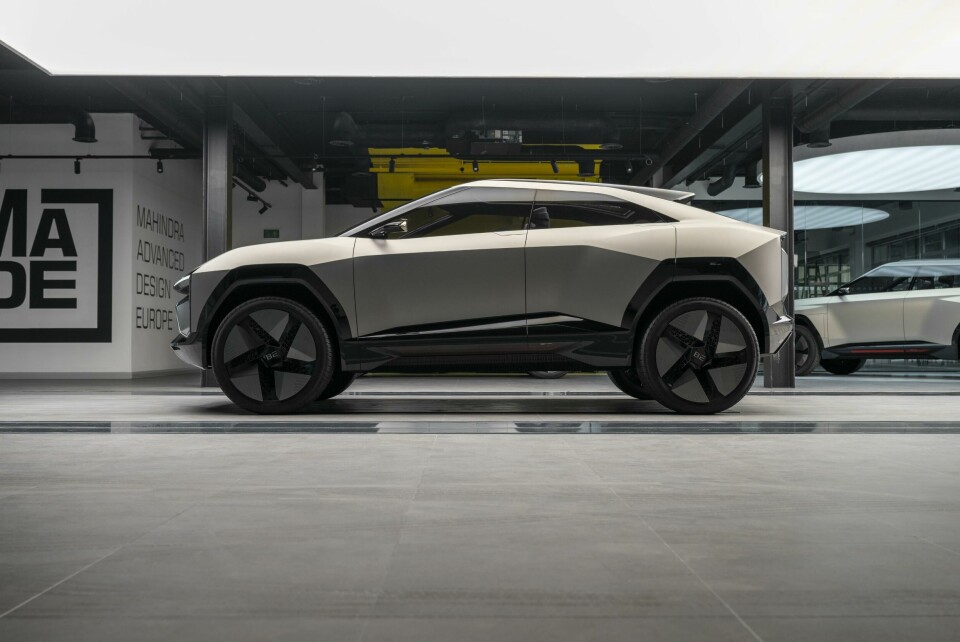
Studio tour: Mahindra Advanced Design Europe
A host of exciting new EVs are being honed at Mahindra’s new UK-based advanced design studio and will soon launch under the XUV and BE nameplates. Car Design News was given a private tour of the new facility and an inside look at its first prototypes
Nestled in an industrial park in Banbury, Oxfordshire, you’d never guess this trendy new studio was once a stuffy call centre — hardly the ideal foundation for conjuring inspirational new designs. But Mahindra’s chief design officer Pratap Bose and incoming studio lead, Cosimo Amadei, immediately saw the potential. “We could see that it had good bones,” said Amadei during a private tour of the site.
It is no concrete goliath, but the site is more than big enough to host end-to-end design activities including conceptualisation, digital and physical modelling, Class-A surfacing, 3D visualisation and HMI design. The surrounding area is also home to an array of other automotive names, including technology suppliers Prodrive and Faurecia, and electric commercial vehicle start-up Arrival. And importantly, it is a stone’s throw from Mahindra Racing (this writer parked there by accident it is so close), so the investment simply made sense.
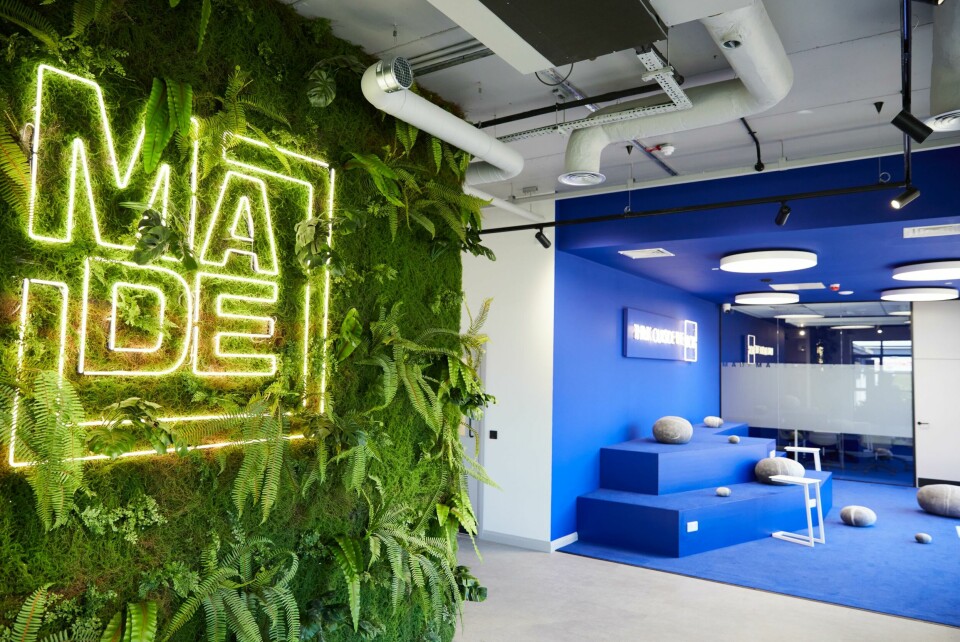
Set across several floors, the Mahindra Advanced Design Europe (MADE) studio was built with openness and creativity in mind. Gone are the days where design bosses are hidden away in a corner office, says Amadei, who along with the other senior design leaders is closely integrated with junior designers, engineering and administrative teams in the same space.
Any formal meeting spaces are made of glass, with discussions occasionally broken up by a friendly nod or wave. A coffee machine at the centre of the middle floor – alongside a wireless speaker through which lo-fi music hums away in the background – invites designers to engage, collaborate and caffeinate in a casual setting. It is a fitting tribute to how the team itself was put together, with Pratap Bose bringing many of the senior designers on board through coffee shop get-togethers.
“This was always designed to be a very intimate studio”
The studio is officially open, but there are still some finishing touches left here and there. “Do you have time for some flatpacking?” jokes Amadei. And he is only half joking – designers have been mucking in with final assembly of the space rather than waiting for contractors. The environment is quite different at MADE compared to other studios he has experienced, more laidback and with a flatter management structure. “This was always designed to be a very intimate studio. If you’ve been in the industry long enough you understand this. You don’t want to have a kind of hierarchy that stifles innovation – people should feel comfortable to report to the chief and speak up.”
A communal kitchen area sits on a separate floor to the main office spaces to avoid the lunch-at-the-desk dynamic (a creativity killer, Amadei explains). A dedicated table tennis area is another sign of the work-life balance Mahindra is trying to cultivate here. “We had to make this a place where people wanted to be. They’re spending a lot of time here, and it can’t all be about work,” says Amadei. “It is a creative job – if you hit a wall, you need a way to reset and refresh. That’s how you produce amazing designs and we can see that it works.” Natural light was also key in this respect, although plans for a huge sky light through the centre of the building was scrapped in favour of speed – a running theme for this studio.
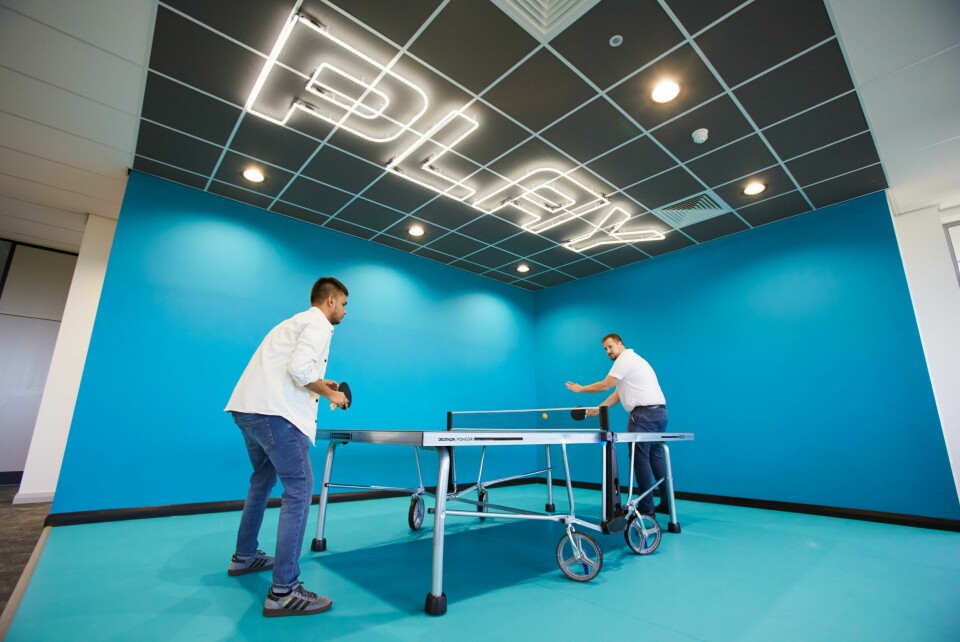
Like any modern workspace, it is less about ranks of desks and instead creating a start-up vibe. Faux shrubbery on the walls? Check. Quirky lighting? Check. Exposed HVAC ducting in the ceiling? You bet. Walls are also adorned with motivational phrases – “do good things”, “think outside the box” and the ever popular “if not now, when?”
It’s a vibrant space, too. The occasional plain white wall is often balanced out with a floor-to-ceiling splash of turquoise, royal blue or bright crimson (Is this really an ex-call centre owned by an Indian manufacturing giant, or the Lynk & Co headquarters in Gothenburg? It certainly feels more like the latter.) Amadei concedes that he lost a fight to have the stairways painted in a similar fashion due to safety regulations, but is thrilled with how the space has turned out overall. Attention was also paid to sustainability, putting waste materials back into use where possible. Large storyboard stands were even constructed using old printer paper.
On the ground floor sits a large meeting room, styled more like a restaurant than a board room, where the design team sat with CDN to reflect on where the studio is at and where it is going.
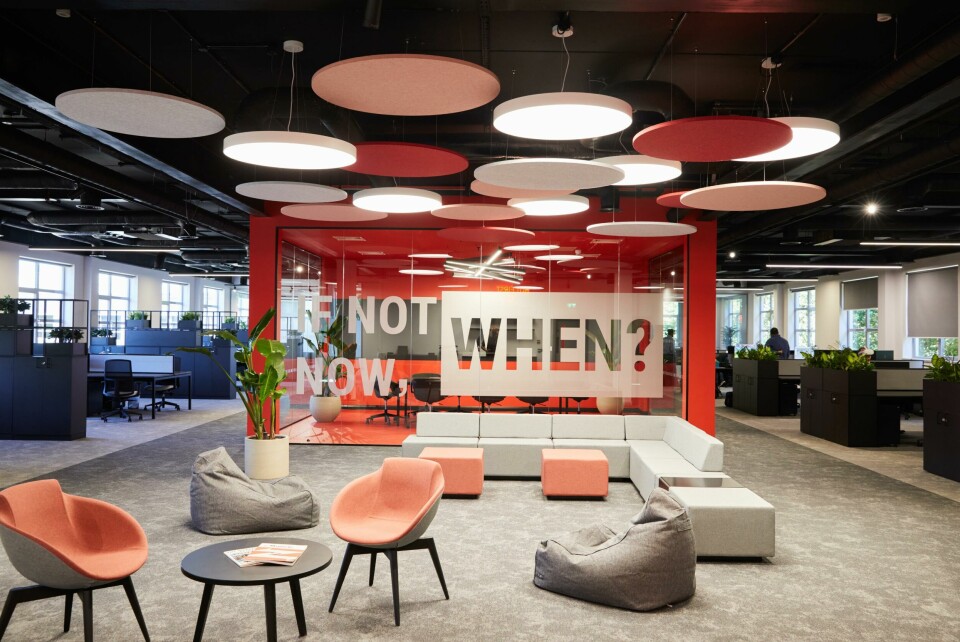
Working side-by-side are many new faces but also old friends and colleagues that have come through the ranks together. While there is no doubt a similar dynamic in many other design studios, the result is a close-knit and undeniably cohesive collection of experts: Paven Patel heads up exteriors and brings experience from JLR; Phillip Gillman leads interiors, with stints at Nio, Lotus and BMW; David Hopwood, an ex-Infiniti designer, heads up CMF and brings nous from the yacht industry.
On the modelling side, Chris Scholes is the CAD chief, another JLR import who worked on the C-X75 supercar; while clay modelling is led by Tom Pitts, an ex-Tata designer. “We’re only a team of three,” he noted, “but we have a very high output.” Simon Clark, chief of studio engineering and Luca Leonora, head of operations, are also prominent figures and were pivotal in getting the studio up and running. “It’s a relatively small team and there is a real family feel about it,” says Clark.
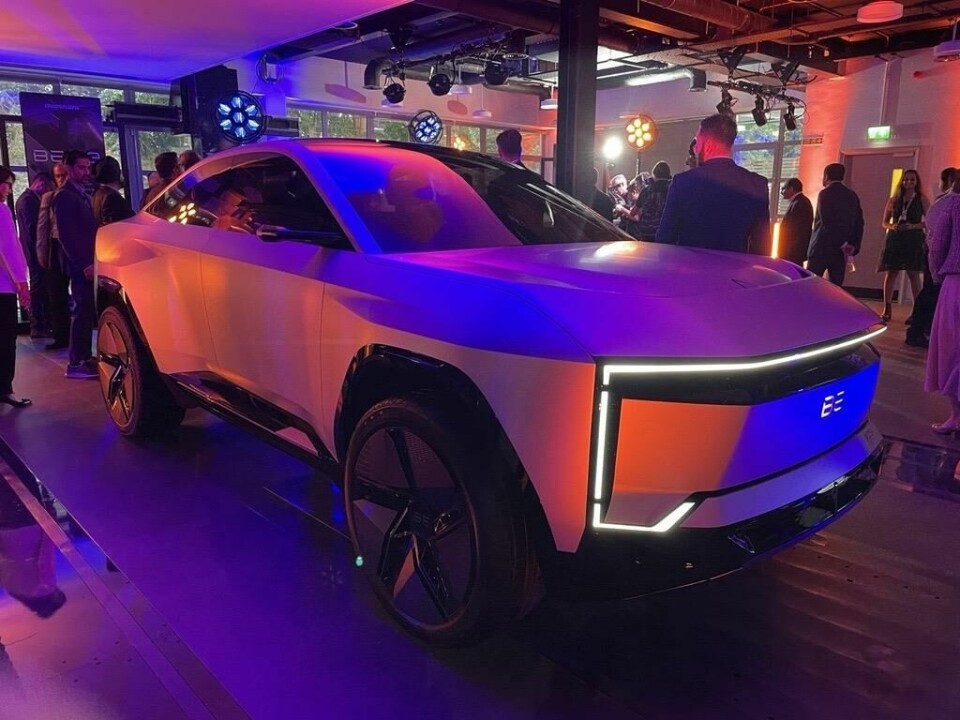
At one end of the room is a full-length projector screen where a promotional video of Mahindra’s upcoming electric SUVs is shown. Choreographed perfectly to coincide with the end of the video, the screen lifts to reveal one of the prototypes, the BE05, on a motor show-style turntable directly behind the glass. Cheesy, but an effective segue from PowerPoint presentations to rolling prototypes, clay models and full-size interior mock-ups. “Make no mistake – this is a proper studio,” says Amadei. Look out for a separate article on the three SUVs on show in this part of the facility, where we take a deep dive into the new ‘Diamond Cut’ design language, architectural inspirations and nods to Mahindra’s Formula E engineering.
”We haven’t got people squirreling away on their own… Everyone is working together”
This workshop is compact but big enough to house several full-size concept vehicles, a static interior mock-up and a milling machine. At the rear of this workshop is an enclosed outdoor area where prototypes can be wheeled out in the open. A balcony on one of the upper floors doubles as a casual meeting area and an aerial viewing station. Everything about the studio is in close proximity by design. The studio aims to be nimble, turning rough ideas into products far quicker than the industry is used to. It is clearly working for Mahindra, with three prototypes created in just 12 months – the BE05, BE07 and BE09. “Our philosophy is to take things quickly to production. Everyone here is a multi-tasker,” says Amadei. “I could tell that everything was going to be done at such a fast pace here,” agreed CAS lead Chris Kerr.
And with the different disciplines of design mixed together – not separated in different offices – the creative juices are well and truly flowing. “We haven’t got people squirreling away on their own here and there,” explains Hopwood. “Everyone is working together on the same project, which is why we have been able to put together these three SUVs so quickly.” It helped that these share the same MEB platform from Volkswagen, of course.
The new studio will sit within Mahindra’s wider global design network that includes sites in Mumbai and Turin via its subsidiary Pininfarina. Shunning the traditional notions of an “advanced” design studio versus a “production” design studio, the new site in Banbury aims to blend both worlds – pushing the boundaries but always with production intent.
MADE is ultimately still very fresh. Team members jokingly refer to themselves by their employee number to describe how recently they joined. The aim is to stay relatively lean – keeping to around 50 employees – but there is no concrete quota in mind. “We don’t want to grow too quickly like some design studios have done in the past. We want to scale accordingly and build up only where we need to,” says Amadei. “If the team gets too large, the management structure changes and the ability for designers to get their ideas on the table is affected.”
The scout for new talent continues but red tape currently prevents MADE from bringing in students from local design schools like Coventry and RCA just yet. The process of securing the necessary approvals to do so is already underway so this should not pose much of an issue, particularly with the talent MADE already has in hand. “It wasn’t that long ago we walked into an empty office. It’s been an amazing journey already,” said Leonora, who helped to coordinate the construction of the studio. “The quality that we have here is really to a global standard,” added Amadei, “with some of the best teams and facilities I have ever experienced.”