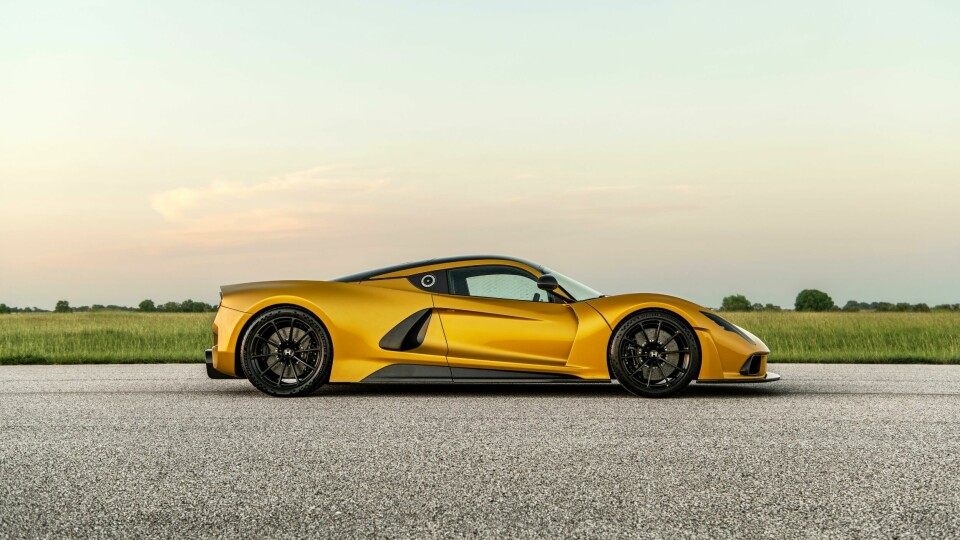
Hennessey’s design director on sketching a 300mph supercar
How do you ensure a car targeting top speed is still beautiful? Over to Hennessey design boss Nathan Malinick
The Hennessey Venom F5 has been designed with one, outlandish goal: to be the fastest production car in the world. Its theoretical 310mph+ top speed will outstrip even Bugatti if it comes to fruition. We chatted to Hennessey’s Director of Design Nathan Malinick to find out whether a car which battles physics so hard can still champion an appealing aesthetic.
Car Design News: How do you balance beauty and science at 300mph?
Nathan Malinick: Our design and engineering teams work hand in hand. It’s not like we progress a design element and then say, “Hey engineering, take a look and see what you think”. Feedback is in real-time. The general shape has to come from somewhere, but there’s feedback from engineering very early on. As soon as we have surfaces to put into an early CFD run, we verify that what’s been sketched also has the potential to meet the goal – which is to be the fastest car in the world. Our next car will be different; F5 has had an unusual level of engineering involvement very early on and then throughout its design process.
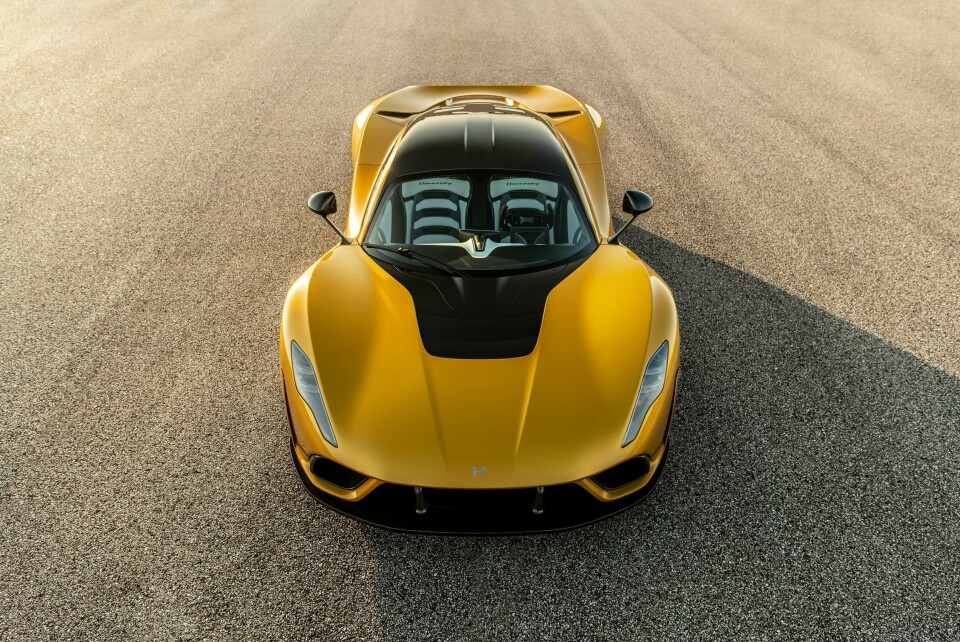
CDN: At what speed does the complexity begin to soar?
NM: There’s an exponential increase in difficulty and complexity beyond 220mph. Most hypercars can do that no problem; 250mph and above remains very, very difficult. You really have to know what you’re doing. Our milestones for 300mph-intent look a little different. We might need to stop and take something into CFD, or rapid prototype something in the wind tunnel before we continue, just so that there’s no time lost. We are a comparatively small company and we have to be extremely efficient. If our target was closer to 200mph then the aerodynamic requirements would be totally different. I mean 200 is still fast, but it’s nothing like 300, which is getting more into the aerospace side of things versus automotive. There is quite a bit of crossover.
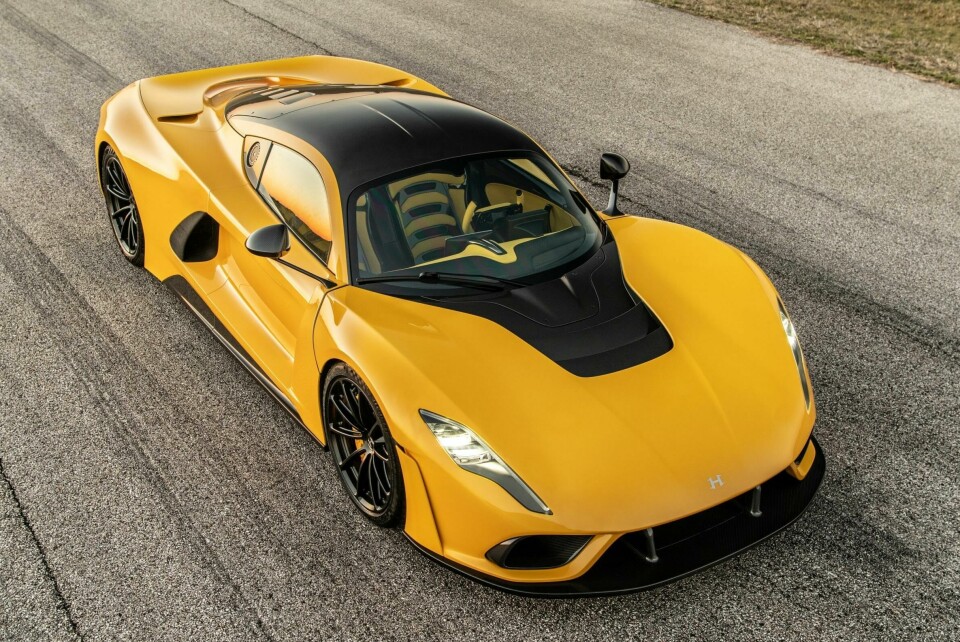
CDN: You have a history in aerospace; how does that help?
Nathan Malinick: The Venom F5 has a lot of aerospace influence inside. From an aesthetic and philosophical standpoint, the interior is relatable to some of the cockpits that I was working on in my previous role. Simplicity drives a lot of what we do; on the exterior, it drove things in maybe unusual ways. One instance would be a lack of active aerodynamics, because we didn’t want to have an aspect of the car that would be susceptible to a failure at such high speeds. No matter what degree you engineer something to, there’s always an inherent risk involved with an active aero piece.
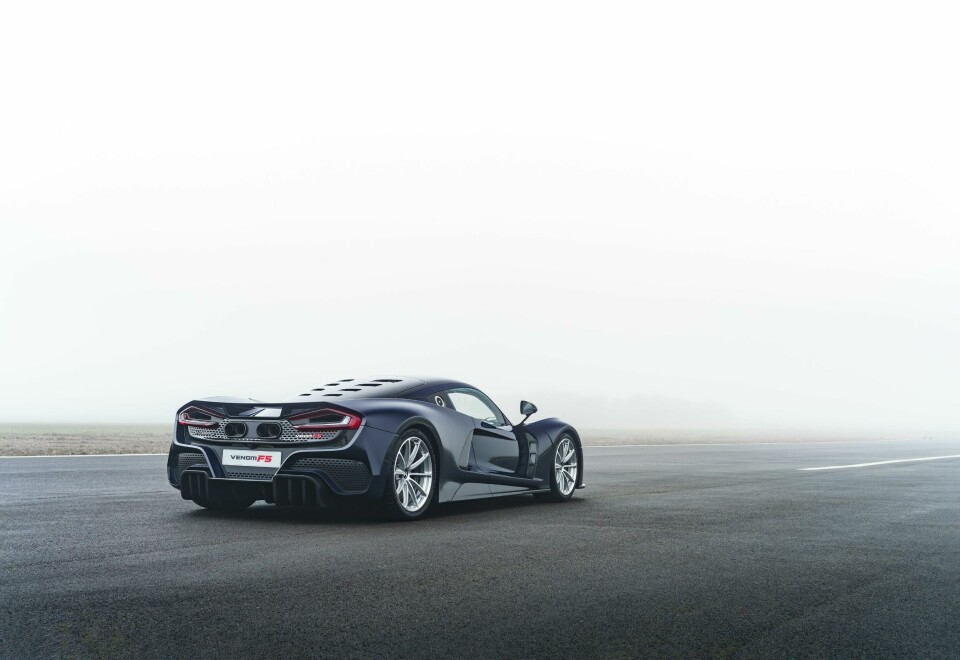
I equate it to some of our military jets. You’re not going to see the flicks and blades of an F1 car on an F-35 or F-22. Likewise, you’re not going to see them on our car because it’s antithetical to its purpose of top speed. Our more trackday-focused F5 Revolution gets a roof scoop, massive rear wing and front dive planes to prioritise downforce and has set a record at Circuit of the Americas.
Pencil and paper do the bulk of the heavy lifting for me
CDN: What role do wind tunnels play in your design work?
NM: The final validation has to be done in wind tunnel, so it’s a bit further down the road. We use it to assess critical stuff like what the car is doing underneath when we pitch and yaw, when we brake hard or mash the throttle. The wind tunnel allows that extra level of fine tuning. But the team right now are validating some items by running them on circuit. A wind tunnel can only get you so far – and talk about an expensive thing! We’re too small to have our own; we use Gene Haas’ F1 wind tunnel in North Carolina. It’s a beautiful facility.
CDN: Is sketching part of such a complex design journey?
NM: I do a ton of sketching. That’s actually my favourite part of the process. I probably have thousands and thousands of sketches, whether it’s F5 or what we’re moving onto next. That’s what I love. Pencil and paper do the bulk of the heavy lifting for me. Very quickly from there, we’ll take it into CAD – whether it’s Alias or Blender – just to really rough out the proportions and translate that 2D sketch into a 3D surface. It’s a pretty efficient process that’s worked well for us so far.
CDN: What is your favourite detail on the F5?
NM: It’s kind of a nerdy one. The bone line on the shoulder of the car is very distinct, and I appreciate it for its simplicity. You can draw the car in side-view with three lines, which makes it easy to understand for a customer or a fan. But within that bone line, the rear fender is beautifully sculpted to a point you go from a proud surface to an undercut, one that creates a really nice reflection on the haunch of the car that’s only visible in certain lights. Every time I see it, I just stop and look.
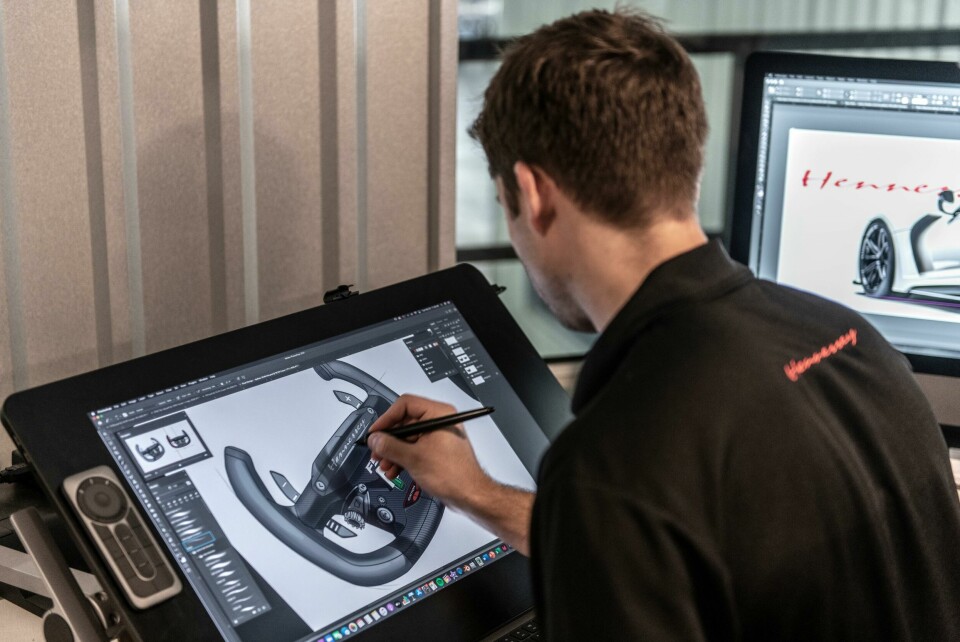
CDN: How easy is it to indulge ideas like that, when the F5’s target is so fixed?
NM: Our engineering team is really helpful in saying “this area of the car is not as significant, so do whatever you want here; if you want to create a reflection here, no problem”. Though sometimes design will be dictated by function. If the front splitter needs to taper like []this[] and there needs to be []these[] flicks underneath, I don’t care. I think some of that is neat: a purely engineering-driven detail underneath the car that you’re not going to see unless it’s jacked up on a lift. And when you do see it, you understand how much went into producing a car like this, making your appreciation even greater.
CDN: Aesthetics still have a place on the drawing board of a ‘top speed’ car, then?
NM: We have creative engineers that recognise the value of design and want to support it, because ultimately people buy with their eyes. Often the first time someone sees our car is on video or in a magazine. It’s got to have that ‘wow’ factor that causes someone to say, “I not only want that, I need that in my collection.” The kind of people we’re talking about already have one of everything. Our car needs to pull on their heart strings.