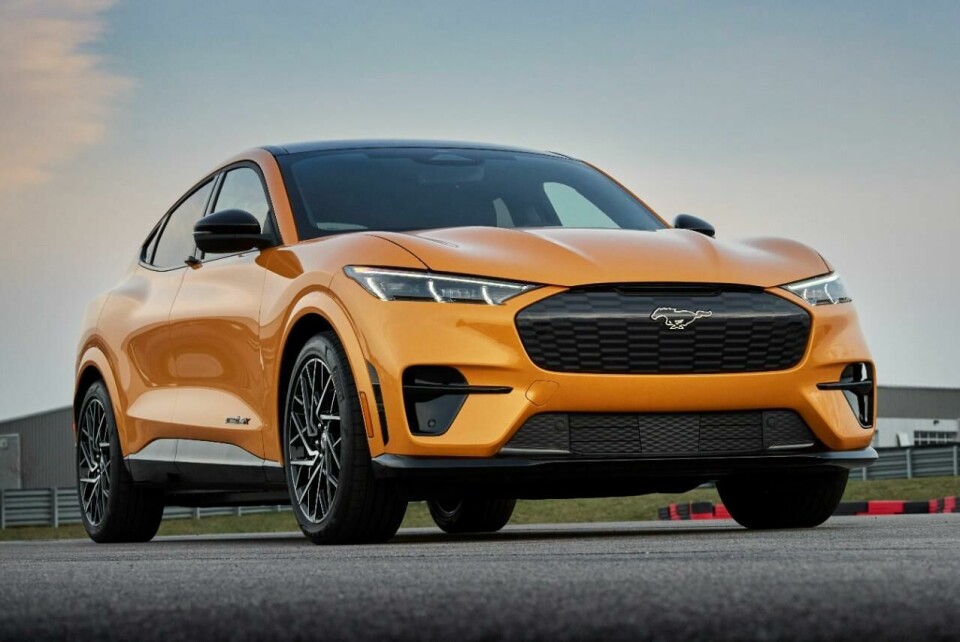
High Voltage: Mustang Mach-E GT
The new Mustang trades the V8 muscle associated with the namplate for a battery-powered crossover. CDN discusses the CMT proposal with lead designer Janet Seymour
Ford goes in search of a new customer base with EV crossover, the Mach-E GT. Car Design News spoke with CMF design manager Janet Seymour who led on the project to discover how this car differed from the Mustang Mach 1, Edge ST and the upcoming next gen Mustang, which she also worked on.
Car Design News: How has your previous work on Mustang and other performance vehicles influenced your colour and materials work on Mustang Mach-E GT?
Janet Seymour: I’ve previously worked on performance vehicles throughout my career in color and materials. Most recently, that includes the Mustang Mach 1 that was just released, as well as our ST line of performance products. Over the years, I’ve been ingrained with an understanding of these products, the brand and performance aspects that contribute to their becoming iconic and enduring. Having had that experience and learning those lessons contributed to the choices our team made for Mustang Mach-E GT.
CDN: What does that mean for material choices?
JS: We were looking at implementing designs that resonate with the Mustang customer. The Mustang is such an iconic vehicle that there’s a certain expectation from customers when they look at it from a materials point of view. It has to look like a performance product, and aluminum is a key attribute that we made sure was incorporated in the Mustang Mach-E GT and GT Performance Edition. We have two levels of color and materials execution that are differentiated between the two products. The aluminum designs with technical patterns and textures are a focal point on the instrument panel that customers can relate to as a key Mustang component. We also incorporated Miko suede to tie into that expectation of performance materials that provide visual texture, as well as grip for functionality. This type of material is typically seen on our performance products and competitor products.
CDN: How do these material considerations for Mustang compare with the expectations of the BEV customer?
JS: While we strived to capture the essence of Mustang that resonates with the traditional base customer, the challenge was creating materials in a more progressive design direction. The BEV customer is very conscious of the impact their vehicle purchase has on the environment. In that sense, it was important to push for as much sustainable recycled material content as possible and make it affordable. We also determined to create an animal-free “vegan” vehicle by not offering leather seats, which is traditionally offered on an ICE Mustang. Yet at the same time, we wanted to create interior material designs with visual impact that customers are excited about and proud to own. For news releases, related materials and high-resolution photos and video, visit www.media.ford.com. 2 In the interior, the seat materials on the Performance Edition are a unique custom registered perforation design with laser-etched patterns and a metallic reflective scrim backing on Miko Suede. The patterns belie a sense of dynamic movement which befits the speed and performance of the Mach-E GT Performance. It is also custom designed to fit the contours of the uniquely designed performance seat. The patterns on the aluminum and the seat materials are all coordinated and intentionally designed with a controlled visual energy that’s relevant to the vehicle’s design language.
CDN: How does the CMT proposition complement the tech and UX?
JS: The materials in the Mach-E GT and GT Performance were selected to support various aspects of technology being introduced in our first all-new BEV. Developing lightweight materials was important to meeting our weight target for range. Every bit of weight counted, so the usage of Miko suede, which is lighter than vinyl, also served a dual purpose as a functional material on seats for grip as part of the performance user experience. The front grille shield on the Mach-E GT Performance was designed aerodynamically with the efficiency of a dual-shot single part for weight reduction, instead of multiple parts to create the illusion of texture and depth.
CDN: Why was aluminium such an important material?
JS: With Mustang being such an iconic vehicle, there’s a certain expectation of materials that are associated with the product and brand. It has to look like a performance product, and aluminum is a key attribute that was incorporated to tie in with customer expectations for genuine materials. Aluminum adds authenticity and a premium quality to the interior. Its cool touch and mechanical appearance correlate with a sense of precision, yet we balanced this with flowing technical patterns and texture that coordinate with the seat materials and interior environment. It’s a focal point on the instrument panel that customers can relate to as a key Mustang component.
CDN: Can you explain more about the choice of copper colour?
JS: We’ve been seeing product and interior color trends shifting towards warm metal tones like Copper, Rose Gold and Bronze for quite some time now. I surmise all OEMs have been grappling with determining direction for a key color signifier on their BEV product line, especially during the past few years of establishing differentiation between their BEV and ICE products. On the Mach-E GT, copper is introduced as part of our BEV color strategy. We recognize the relevance of all its natural properties and how it relates to electric vehicle technology. Real copper also has varying range of hue and value. This allows us flexibility to develop a range of finishes within the copper color family, so we’re able to support appropriately for various segment products and brand. For example, copper on a Lincoln BEV could vary from Mach-E GT.
CDN: How is the role of CMT designer changing?
JS: Generally, I see a shift in all product industries in which the CMF designer plays an increasingly vital role in the product development creation process. It’s great to see CMF is no longer an afterthought, and less of a decorative application after form creation. I and my team are engaged up front and throughout the full design development process, working collaboratively with our x-functional design team to define colors, materials and finishes as it relates to the form language. There are instances where the form must change due to material processes, which results in a material led design execution. My education and background are industrial design, so I’ve always been conscious of envisioning the overall product goals inclusive of form, function and creating desire. It’s been encouraging to see designers at all levels embracing CMF design, learning about all the various material commodities and processes, its capabilities and limitations, and understanding how color and materials can influence the design direction.