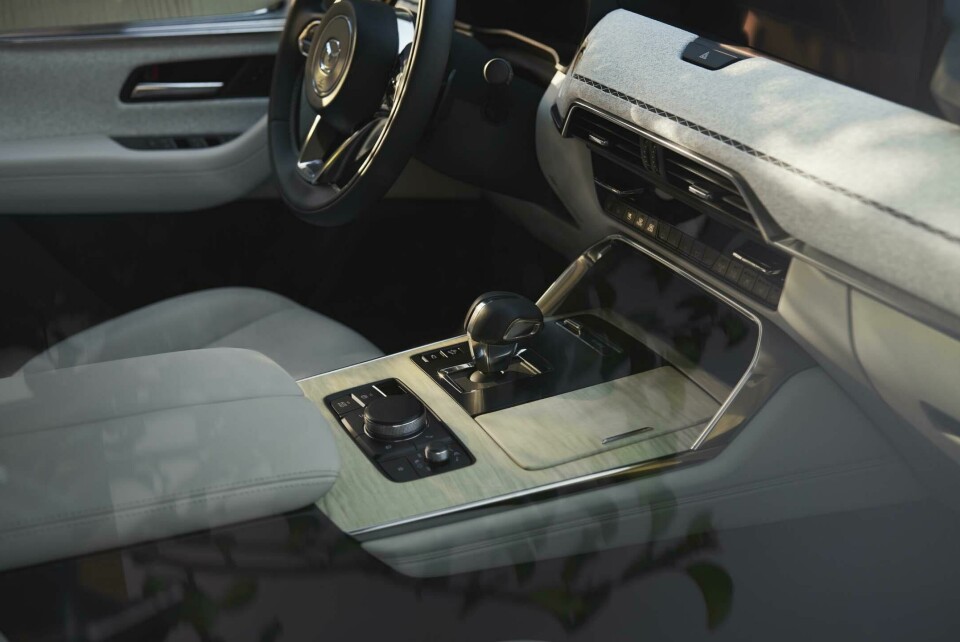
Interview: Alena Gersonde, senior colour and material designer, Mazda Motor Europe
From a spell working as a motorsport journalist to shaping the look and feel of new cars, the German-Italian designer discusses the collaborative aspect of CMF, smart surfaces and transporting European flavours to Japan
Mazda is well and truly embedded in the premium segment these days and one of its latest models, the flagship CX-80 SUV (and in the US, the CX-90) epitomises the brand’s attention to detail.
From the lustrous paint on the outside to the calming mix of materials inside, much of the final look and feel is influenced by the CMF team both at HQ in Japan but also the European studio just outside Frankfurt. We caught up with one of the rising stars from the latter, Alena Gersonde, who spoke about collaboration, trying new things and the nuances of CMF design between different brands.
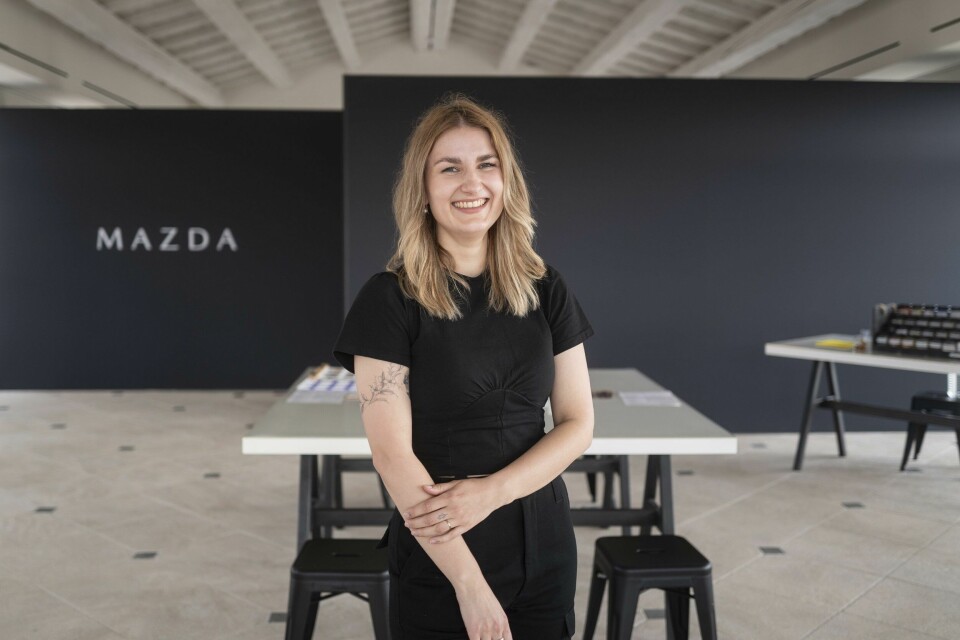
Car Design News: You had a brief spell covering Formula 1 as a journalist before moving into the CMF world. That seems like quite the jump!
Alena Gersonde: Yeah. It was at a time where blogs were quite big, and, as someone who was in the sphere of motorsport fans online, I wrote a test article for one outlet and it went from there.
CDN: At that time, did you still have plans to get into CMF? Were you even studying CMF?
AG: I was always drawing and sketching as a child, and my little journalism journey was mainly about finding people I could talk about motorsport with. The design aspect, or the art aspect, was always what I had in mind. After some time in Italy I considered all of my options and went to study design, because I felt it was closest to heart. Even though I loved the motorsport circle, design felt more in my comfort zone.
CDN: Where did you study?
AG: I studied at the technical school for product design in Selb, Germany, which is famous for clay modelling. There were lots of workshops with different OEMs going on, and I often snuck in, talking to the experts that came to visit, handing them over my portfolio…
CDN: So even as you were learning the ropes of CMF, you were also dabbling in clay modelling?
AG: During my first year, we did everything. To be honest, I found the hard modelling part quite nerve wracking because I generally prefer to be able to correct my work and redo it over and over if needed.
Everything is quite mixed, and I think that helps. It’s an relaxing, open atmosphere
CDN: But has that general understanding of the clay modelling process helped you in your role at Mazda now, would you say?
AG: I think it really helps to respect what modellers do. When I was studying, I was always in the clay studio when I had free time – it’s an amazing craft and I really enjoy what they do. I’m definitely no expert, but I know at least how hard it is to come up with those beautiful surfaces. I always try to keep up with what’s going on in modelling, and I really appreciate working with our complete modelling team at Mazda. It’s a great team and we do a lot of projects together. Without them, I wouldn’t be here.
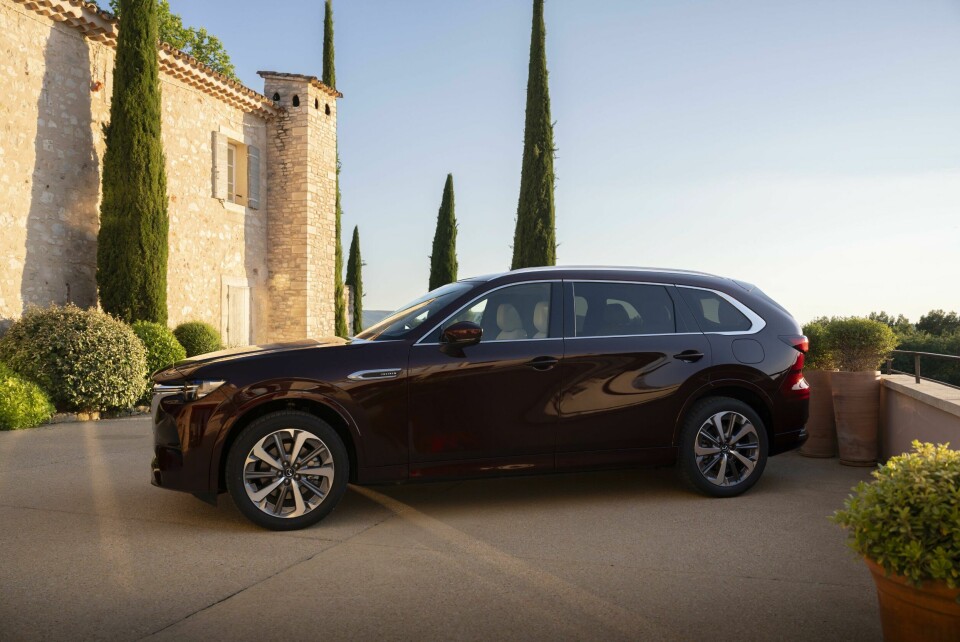
CDN: Beyond that, I would imagine that the CMF team interacts with pretty much all teams in some capacity?
AG: Exactly. We have an open floor in the studio, so we all talk, gather and work on projects together. On the ground floor we have a lot of workshops – or play rooms as I think of them – but also a little painting room, so basically everything that our modellers need. At the moment we have a fairly tight knit colour and trim team, but generally speaking everything is quite mixed, and I think that helps. It’s an relaxing, open atmosphere.
CDN: Before coming to Mazda you also spent time with contract manufacturer Magna Steyr. How did that experience compare?
AG: The overall goal of the team was quite different. We still had an open floor and everyone was mixed together, but you could not always work with everyone together. For example if one client just wanted colour and material support, for example, or another one just wanted some modelling.
CDN: What does the relationship look like between Mazda’s European studio and the main site in Japan – what is your mission?
AG: Generally speaking, we are here to explore and take the time to really look deeply into topics in a way that the Japanese team might not. There is an advanced design team in Japan too which is doing some amazing output, so we are more of a support to the production team to help them be successful with their development.
CDN: And you must be based in Frankfurt for a reason as well. You want to give them a European flavour.
AG: Exactly, but we are also showing how to transport the Japanese feeling into Europe, too. We sometimes have the opportunity to go together to certain events; at Milan design week, for example, we usually have colleagues from Japan coming to cover trends and we are able to compare and contrast what we took away.
CDN: Are they quite different takeaways?
AG: Yes. But it makes sense, and this is really what makes the richness of this corporation work. This kind of sharing is what you need to do if you’re working globally and want to understand the market’s demands.
I see a lot of possibilities to explore materials that have been forgotten over the years
CDN: Reflecting on your field of design as a whole, do you feel there’s more recognition of CMF these days in the overall development process?
AG: Looking at the industry, I do think it’s changing. I do not recall reading so much about colour and material designers in the past – I didn’t even know it existed when I was younger, even though I’ve been into cars all my life. There are even developments where you can almost see how CMF was key from the very beginning. Like the MX-30, for example, where we integrated cork in the interior.

CDN: Is this growing role a convergence of trends – EVs mean there is less brand differentiation around the engine, and premium trims are filtering down into entry level cars.
AG: Probably. And I aspect is that if you were focusing a lot on the sound of the engine before, you also had a little bit more distraction. Even though Mazda is still a very driver-focused manufacturer, we are trying to create new experiences alongside that like around craftsmanship and haptics from the materials. There’s a lot of room to play in this respect.
CDN: We are seeing smart surfaces come in where functions are hidden until needed. Has that brought you closer with the UX teams?
AG: You always appreciate what others are doing, and I’m going to try to learn as much as possible so that we can create the most beautiful product together. It’s of course a topic that is extremely interesting and investigating solutions for, but I don’t want to give away too much.
CDN: If we get the crystal ball out, are there any particularly promising new materials we should expect to see coming in?
AG: Yes and no. Since we’re so early in the design exploration we usually have more of a range of options to choose from. But I’m also a big fan of a ‘back to the basics’ mentality: fabrics have had this image of being the base option – slap on a black fabric and call it a day – but I think there are a lot of possibilities to really work on fabrics and all of these soft materials that have been a staple of interior design forever.
I really want to explore these super-logical solutions that maybe don’t sound as fancy as some of the new alternatives being spoken about, but to expand on has been forgotten over the years.