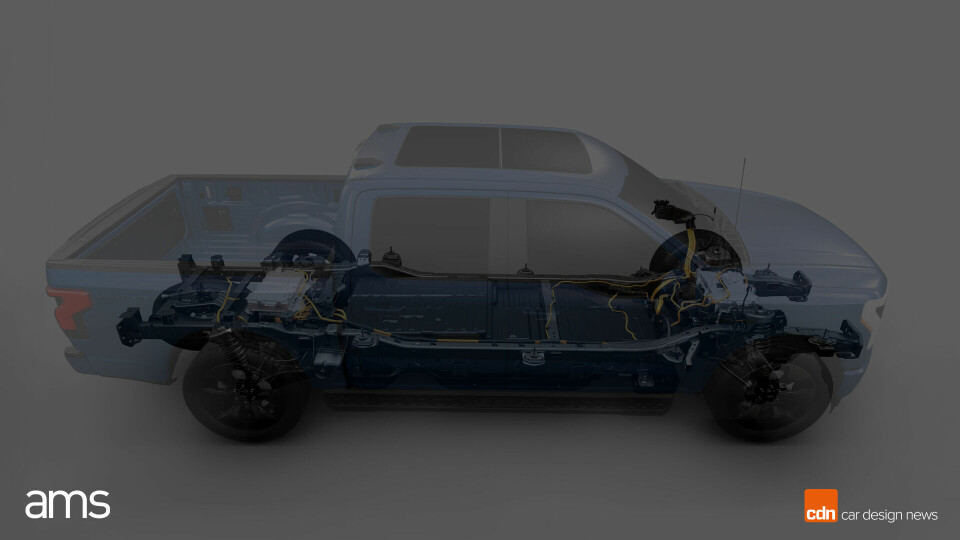
Lightening the Ford F-150 Lightning
As truck buyers increasingly scrutinise range, Ford’s design team had to pay close attention to lightweighting in realising the OEMs gamechanging F-150 Lightning
At CDN’s sister title Automotive Manufacturing Solutions Livestream Hour – Lightweighting next-gen vehicles – design and engineering experts from Ford discussed the latest challenges and wins in reducing vehicle weight through new material choices, manufacturing techniques and vehicle redesign. Scott Anderson, Ford’s lead interior designer for SUVs and trucks, said lightweighting was a top issue as consumers looked at range as a critical factor in their choice of battery electric vehicle (BEV). That is certainly the case in the choice of the ever-popular pickup truck in the US and Ford has made some advanced structural weight saving in the electrification of its Ford F-150 – the Lightning.
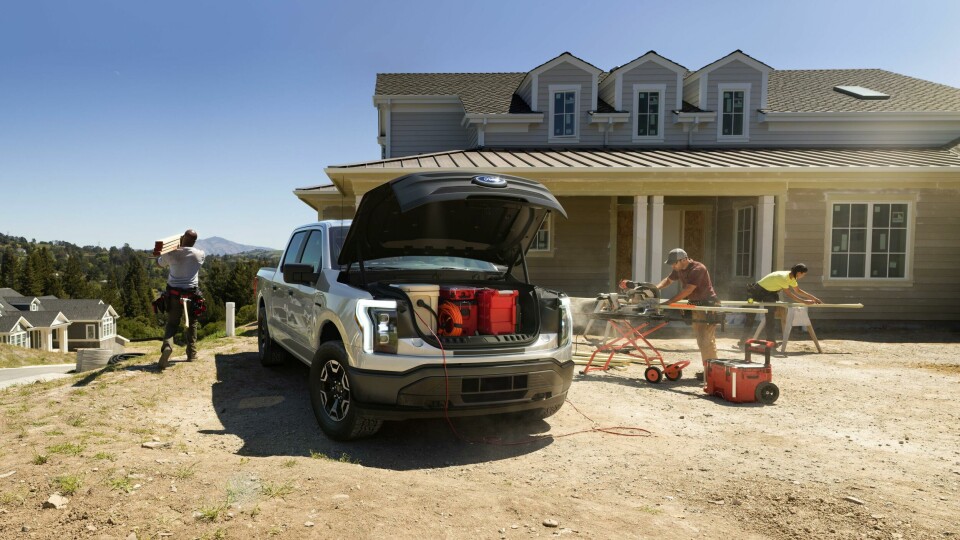
Ford’s F-series is the most popular pickup in the US (and has been for almost 40 years), so convincing the public that an electric version is as good as that one driven by an internal combustion engine (ICE) is crucial to the carmaker’s continued success with it. As well as saving to accommodate the extra weight of the battery, Ford had to maintain the range, power and cargo capacity, which are all selling points for a pickup.
“Lightweighting played a huge role for us on the Lightning programme,” said Anderson’s colleague Elvir Mesalic, senior exterior designer at Ford. “Repackaging the legacy platform that was handed down to us from the ICE F-150 meant we had to get creative. We had a limited budget [but] had to find more cargo space and enhance load capacity.”
The absence of a combustion engine in the front of the vehicle allowed Ford to reconceptualise a front trunk – or ‘frunk’ as Mesalic called it – to meet the functional need for storage space and to achieve best-in-class cargo volume. Productivity, durability and serviceability were the three key demands.
“We built the side walls and floor [of the frunk] with a compression-moulded sheet metal compound, that is pretty strong and very light,” explained Mesalic. “We had a scuff plate that needed to be integrated in the SMC [sheet moulding compound] and that enabled us to tighten the gaps. It also helped achieve a higher load-weight capacity just by minimising the weight.”
Mesalic’s team also identified that it could take four out of the five metal brackets that were sitting under the floor of the frunk, where were legacy components from the ICE version of the F-150.
“By eliminating those four brackets not only did we save weight, we were able to lower the scuff plate and the Z-height, also by integrating a waterfall grill, which enabled us to create a very low entry point for the frunk,” explained Mesalic. The Z-trim height determines the proper ride height for the front end of the vehicle.
While finding these savings, Mesalic’s team was on a tight budget and could not resort to expensive high-tech materials. It was more a case of carving out weight across a number of different areas.
“To achieve lower load height, for instance, we used the B side of the scuff plate, ran CAD analysis and really made sure that the minimum requirements were taken care of but also that any extra weight was carved out,” explained Mesalic. “The sum of all these little areas, where we carved out weight, made a big difference.”

Limitations led to a greater focus on innovative solutions and the same was the case on the development of the Maverick compact hybrid truck. According to Anderson, creativity in the absence of constraint can breed inefficiency. He said being forced by a low price point and fast development schedule provides a licence to try new things and the programme for the Maverick was the fastest ever completed at Ford. It has now become the new template for the company.
The interior concept of the Maverick is pared down and reductive, and it showcases the structure of the vehicle’s body and the sustainable materials used to construct it. In doing so saves weight by removing parts that do not need to exist.