2020 Trend Report by CnTFactory
Trends forecasters CnTFactory catalogue the interesting trends for automotive designers
The CnTFactory team hunts for innovations and new materials in fields such as architecture, fashion, design and lifestyle, and identifies forthcoming trends for the automotive design community. CnTFactory is now bringing its expertise to Interior Motives: here are its top five colour and trim trends for 2020 and beyond, plus highlights from the 2019 Dutch Design Week
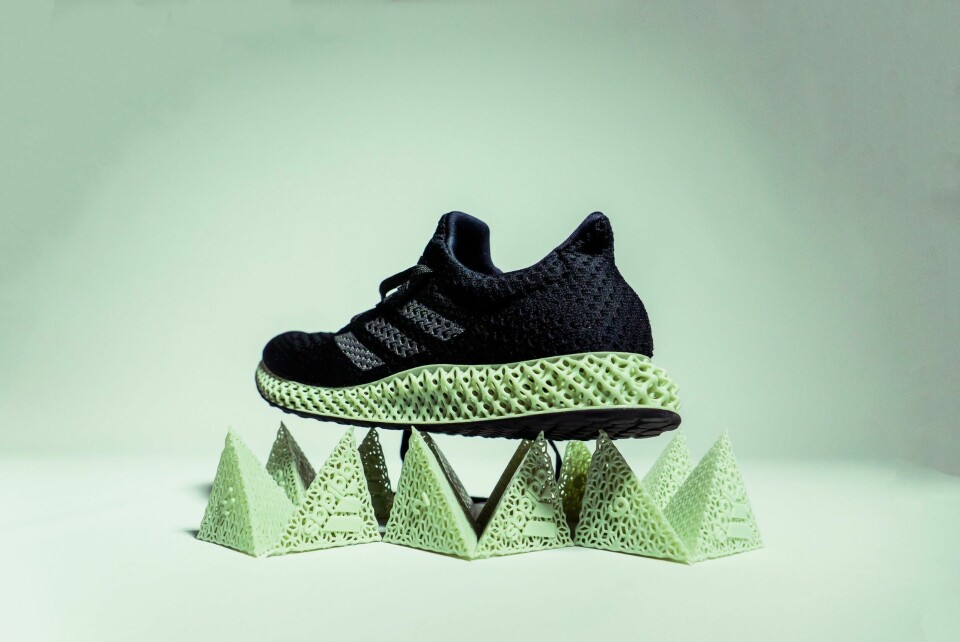
Digitisation of colour, material and fabric
Technological advances in laser cutting or 3D printing have opened new design possibilities for aesthetic appearance, weave graphics and manufacturing. Not only great for creative freedom and easier experimentation, digitally-infused manufacturing methods reduce building constraints and, depending on the material used, give any creation visual structural integrity. We expect to see digitisation revolutionise production processes, eliminating expensive tooling costs, adding flexibility to enable high levels of customisation, and allowing much faster design alteration. Developing an underlying structure and applying materials is going to become one process to merge form and function. Digital Light Synthesis (DLS), developed by Silicon Valley firm Carbon, is used for the soles of the Futurecraft 4D running shoes [above]. This technique uses light to shape a specially developed liquid resin that has elastic properties, then heat to set the material. Unlike 3D printing, which uses solid plastic, the DLS process employs a liquid polymer – shaped by natural elements – to give a lighter, more comfortable shoe. The fluid reacts to light and oxygen by hardening, yet remaining solvent. 3D printed, laser-cut, algorithm-defined pieces form the latest collection [below, gallery] from Dutch haute couture designer Iris van Herpen. Gradient-dyed silks are multi-layered into sculptural shapes by a fine 3D laser-cut frame of PETG (polyethylene terephthalate). Configurable carbon and metal 3D printed interior finishes form a beautiful central ‘saddle’ which features in a unique parametric inter-locking form in the Aston Martin DBS GT Zagato [below, gallery]. This is available in three materials and finishes: printed carbon, aluminium, or gold PVD (Physical Vapour Deposition).
Space Material
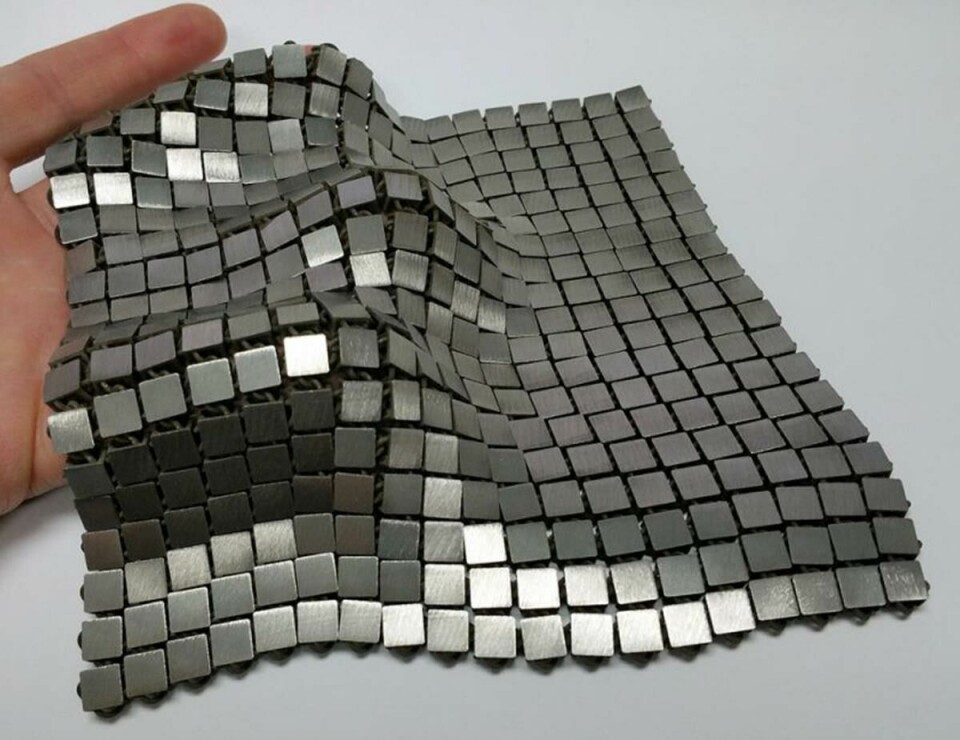
Popular figures like Elon Musk, who has been demonstrating the SpaceX reusable rocket launch system, have heightened interest in the high-tech world of space exploration again. NASA is thinking beyond static structures and materials with 4D printing technology for metals or plastics whose inherent material characteristics make them unfold at a certain heat, or expand and contract under certain environmental conditions. NASA’s space fabric [above] has flexible geometry that can both reflect and radiate heat. Inlays made from meteorite material [below right] are offered in BMW’s Individual Manufaktur bespoke trim programme, designed in collaboration with the Max Planck Institute for Extraterrestrial Physics. These can feature in areas such as the centre console’s trim plate and the engine’s start/stop button. Distinctive geometric straight-lined structures, known as Widmanstätten patterns, occur naturally on the surface of extraterrestrial objects such as meteorites. These have the appearance of ice crystals and become visible when certain types of iron meteorite are polished or brought into contact with acidic compounds [gallery below].
3D knit textiles
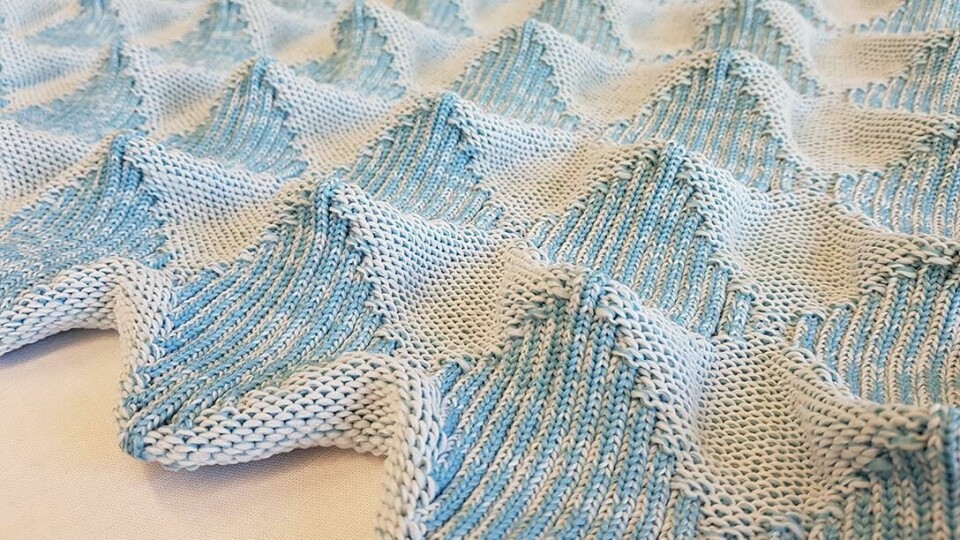
The sportswear industry has spearheaded a revolutionary shift in textiles to 3D knitting and Knitposites. One new technique applies heat in the knitting process to create a jewel-like armoured exoskeleton which is both structural and soft in certain areas as required. The combination of lightweight flyknit construction with heat-moulded yarns allows the addition of structure and colour. The result is a durable, supportive and stretch-resistant surface. Designers can experiment more freely, trying ‘fit to form’ concepts with much more complex fabrics. Growing awareness of the need to develop more sustainable fabrics is driving the use of plastic ocean waste, recycled fibres, or simply more natural fibres. Such possibilities bring renewed interest in environmentally responsible alternative textiles with premium and high-tech appeal. Industries not commonly known for their innovative use of fabrics are starting to embrace these for their limitless graphic opportunities, tactility and visual differentiation.
Beyond paint
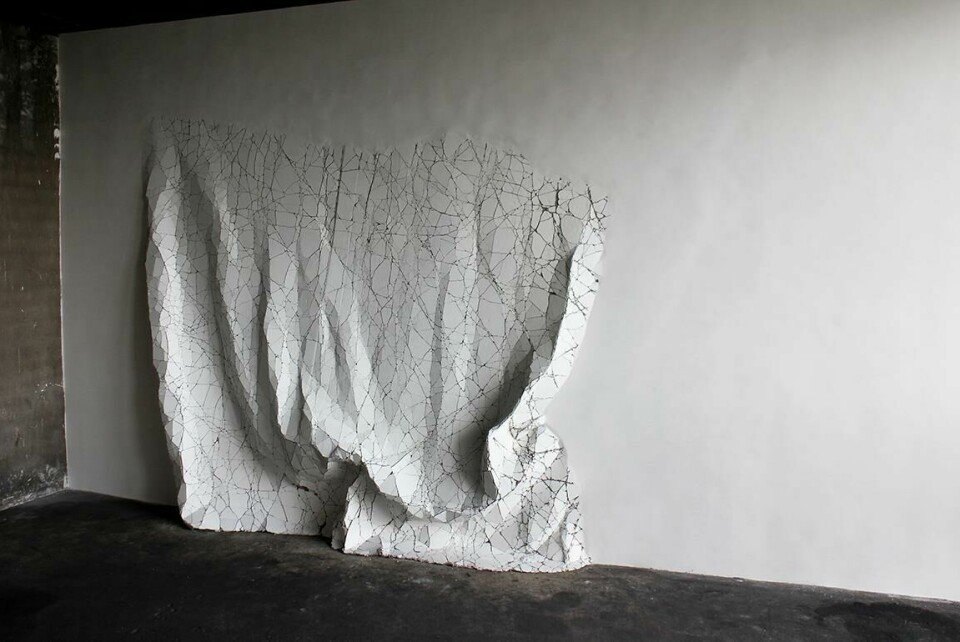
After solid, metallic and satin finishes, textured paints are now making a bold entrance into the design world, enhancing visual appearance with their tactile aspect. Various new texture effects, such as plaster, velvet, concrete or even recycled plastic, add powerful interest to a product’s surface. Mineral Fabric by textile designer Elfie Poiré [above] is in perpetual motion on even seemingly inert subjects. Her experimental approach seeks to make visible the underground and mysterious forces that shape reliefs, folds, ruptures or cracks. New paint technologies are emerging with special pigments allowing functionalities like conductivity, light absorption, reflectivity, soft-touch effects or even volatile organic compound absorption [gallery below]. Light-absorbing “ultimate black” Vantablack, featuring carbon nanotubes, was seen on the BMW X6 [gallery below] at the 2019 Frankfurt motor show.
The repurposing loop
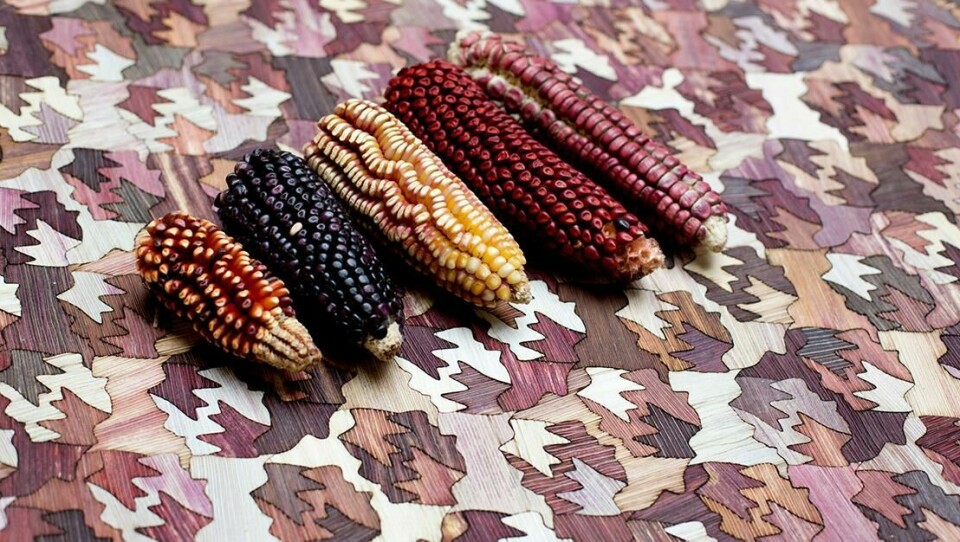
Repurposing gives material waste a second life, and combining existing natural products with smart designs gives the potential to find solutions to reduce waste in the first instance. Scientists, engineers and designers are working together to bring alternative eco-friendly materials to market. Designer Fernando Laposse hopes his Totomoxtle material [above], a veneer made from waste husks of heirloom varieties of corn, will support biodiversity and regenerate traditional agricultural practices in Mexico. Biofabrication is a biological manufacturing process on a cellular or molecular level to create lab-grown materials to replace petrochemical-based products. Piñatex has created a natural textile from pineapple leaf fibre [gallery below pale material] which can be substituted for both leather and PVC; and US biofabrication firm Modern Meadow has launched a brand called Zoa, which uses collagen protein as the core building block for its textiles [below, blue]. A project at French think-tank lab Atelier Luma has mixed specially-grown micro- and macro-algae with biopolymers, then 3D printed this material to give a creative alternative to oil-based plastics [gallery below].
Dutch Design Week 2019
At DDW19 (Eindhoven, the Netherlands, 19-27 October), many of the artists’ exhibits were on display in the city’s repurposed industrial buildings. Befitting this, many aimed to tackle the question about how to make smart use of resources. It is exhilarating to see a rethinking in sustainable future products that echoes the urgency being felt across design education, industry and the customer base alike. Renewable and recycled materials, repurposed waste and biomaterials bring their own aesthetics to the design world.
Linescapes: The textile art studio Fault Lines, founded by Matthias de Vogel in 2015, experiments with traditional ideas of textile art and reinterprets them in a new way. Linescapes are handwoven panels of tactile depth, with bold graphics in grids and geometric structures. These compositions are inspired by the beauty and richness of weaving techniques from craftspeople in India, Morocco, Turkey, New Mexico, Japan and Scandinavia.
Comfort zones: Maria Wolff Metternich has explored both physical and emotional comfort/discomfort: a variety of Comfort Zones deal with the delicate relationship between filling material and cover, to form knitted structures and materials and appear soothing and comfortable. The elasticity of the knit shows graphically over the volumes in a decorative way in, for example, furniture applications.
Interactive dining table: The social experience of sitting together is graphically enhanced by this table with its embedded load cells and LED lights. The load cells respond in colour and brightness to weight shifts on the table top, and the table records and interprets the behaviour of, and social interactions between, those seated there. It was created by a team at the University of Twente as part of a personalised e-health technology research programme.
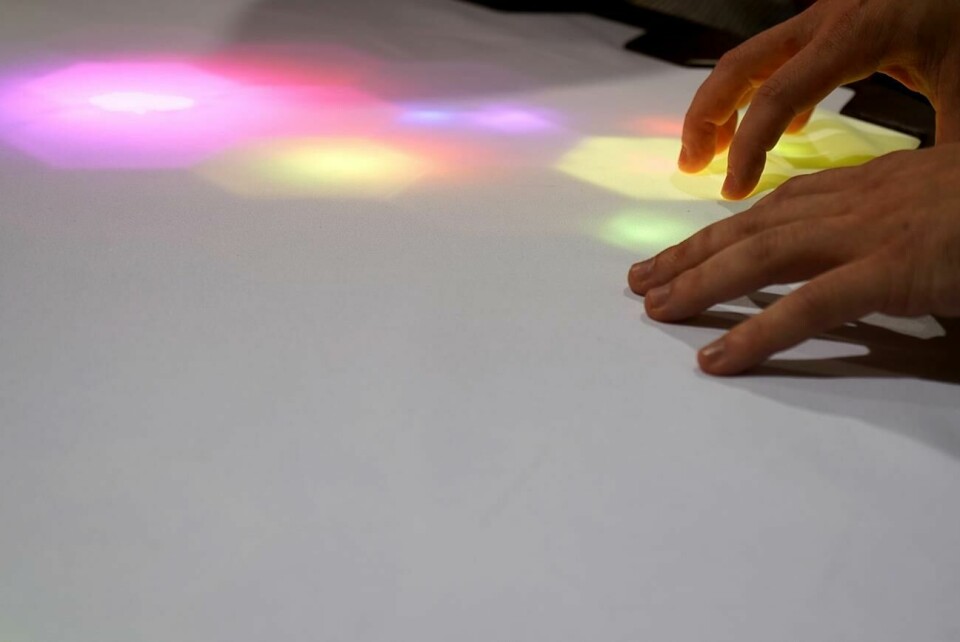
Waste No More: US fashion label Eileen Fisher started a take-back programme in 2009 as part of a circular system designed to preserve the value of clothes at every stage, in any condition. Over 1.2 million garments have since been collected, and pieces beyond repair become raw material for Waste No More (WNM). Led by creative director Sigi Ahl, the WNM studio transforms damaged clothes into one-of-a-kind artworks, pillows, wall hangings and accessories using a custom felting technique that requires no water or dyes.
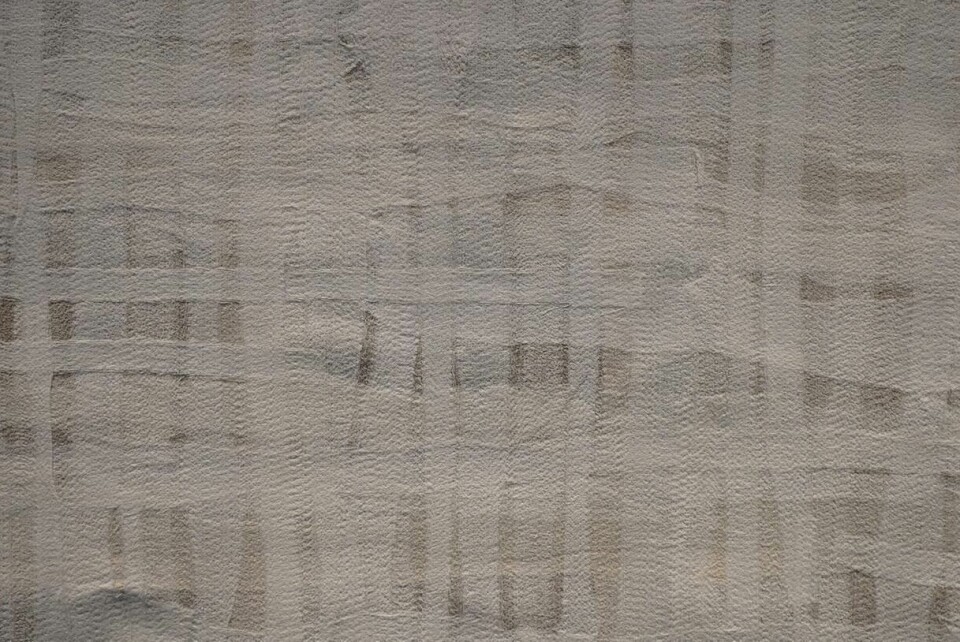
Woven braids: Polish-born, Delft-based designer Aleksandra Gaca (who created the interior fabrics for the Renault Symbioz concept car) has channelled her research into braid patterns, constructions and traditional textile techniques into a new series of fabrics titled Woven Braids. These vary from 3D-woven acoustic textiles to flat fabrics used for tea towels; they are woven with sustainable yarns and manufactured in the TextielLab, Tilburg.
Foamation: French-American designer Steven Akoun’s glass foam is created with sustainable materials such as recycled glass and uses eggshells as a mineral foaming agent. The result is a stunning lightweight structure which, as wall tiles, has sound-absorbing characteristics.
For more inspiration from CnTFactory, visit www.cntfactory.com or follow @cntfactory on Instagram. The next report will feature in the Spring 2020 edition of Interior Motives magazine. Subscribe here.