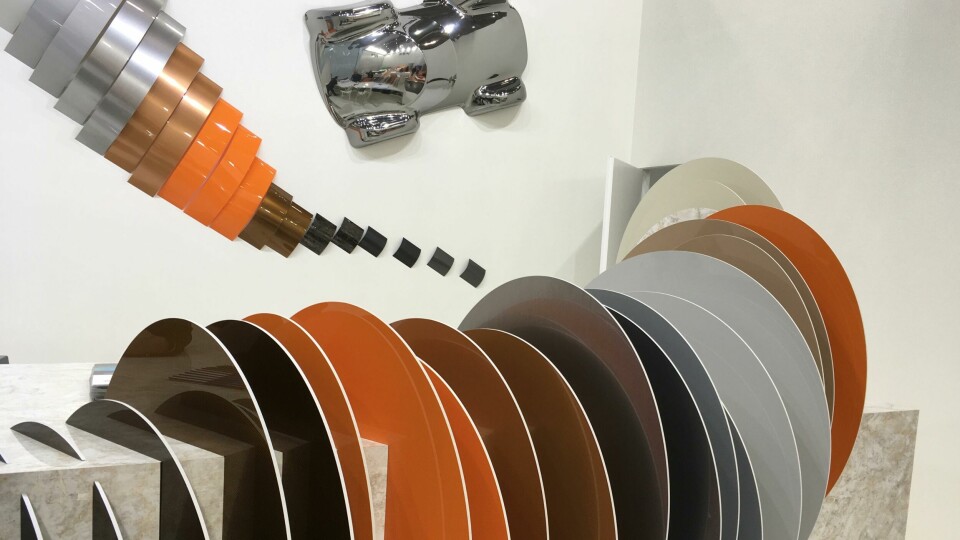
Show Review: K 2019
A place for plastics in automotive design
The plastics industry is very keen to talk about how it is embracing the so-called circular economy, sourcing sustainable raw materials and developing products which are recyclable at end-of-life: major themes at K 2019, an immense trade fair in Düsseldorf, Germany, with over 3000 exhibitors from 60 countries. Presentations, lectures and workshops discussed issues such as marine litter and packaging waste, while vast whirring machines demonstrated how to sort, shred, reconstitute and then spit out new polymers and second-life products. With plastic production rising worldwide (to 348 million tonnes in 2017, according to Plastics Europe) it is ever-more important to address the way plastic is manufactured, used and then recycled or repurposed.
The automotive sector, which currently accounts for 10% of plastic output, is heavily implicated: plastics are deployed to save vehicle weight, in particular, and are expected to become more prevalent as electric vehicle production grows, to help conserve battery range. Designers will therefore be increasingly working with plastics and need to consider their role in the vehicles of the future.
Covestro interior concept
“New mobility concepts will lead to different designs of cars,” said Markus Steilemann, CEO of Covestro, one of the largest polymer suppliers. “Individual mobility will not disappear, nor mobility supported by passenger vehicles, but we have to think again in different contexts. Today, 50% of the volume in a car is plastics, but just 10% of weight; now, with electromobility, connectivity and autonomy, this is relevant to the idea of a vehicle for different contexts and situations.”
Covestro unveiled a vehicle interior showcasing how its materials can support the creation of the car as a multifunctional living and working space. “Mobility must become more efficient,” said project leader Jochen Hardt, saying that when people spend hours in traffic, they should utilise this time in a valuable way; and that the car should adapt and adjust to user needs and customer expectations in driven, shared or autonomous modes. “It should fit into modern digital life,” he stressed.
The “very pure and slim” design theme was created for Covestro by Miika Heikkinen of Northern Works, Turku, Finland, to highlight the materials. Most notable is the large, curved polycarbonate display, integrating two screens; along with active screens in the windows and smart surfaces, this reduces the bulk of an IP. Created with partners including Continental and Kurz, its cover plate of Covestro’s Makrolon Ai polycarbonate and Makrofol foil offers excellent screen resolution and is claimed to be very strong. Similar materials are used in the overhead control panel, developed with Tactotek, which features embedded LEDs and Makrolon resin between two films. “We inject the resin materials, put the films together, and use Makrolon to get stiffness and transparency for the light guides,” explained project manager Jan Helmig. “It’s extremely thin.” Such polycarbonate films can further contain printed electronics.
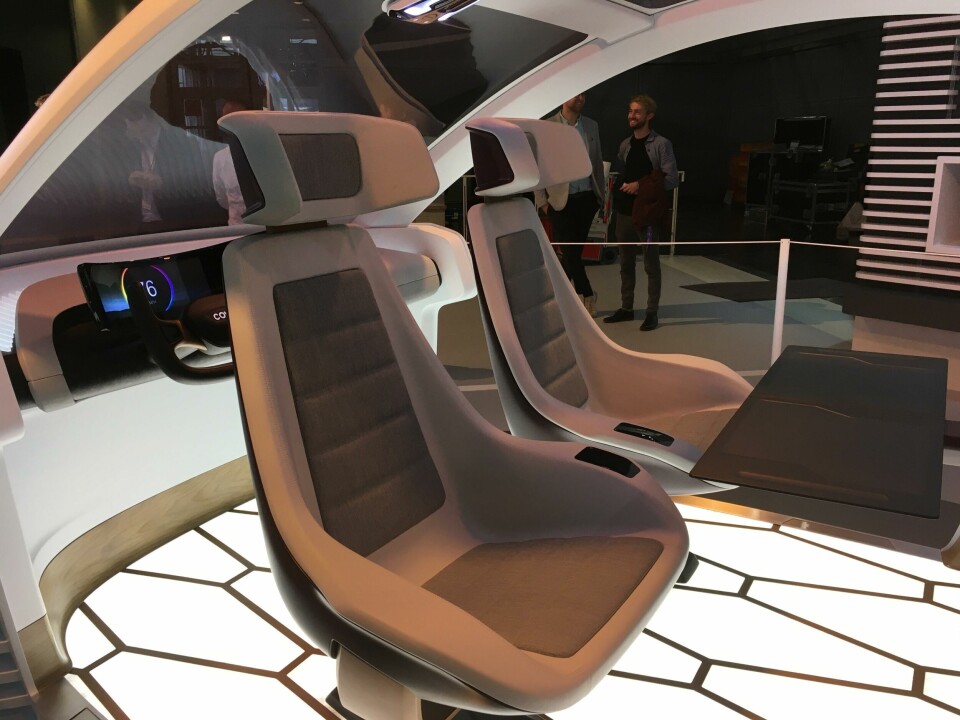
The concept’s seats showcase a polycarbonate composite called Maezio. “We thought how to make a lightweight and stable structure out of our materials: coatings from our raw materials, and then the whole shell out of our carbon composite, in a sandwich structure,” said Helmig. “It also gives a very good surface quality; you can paint it very easily.” Over the centre structure and foam, a water-based (non-solvent) textile coating called Insqin is applied for an artificial leather effect. “This is translucent; you can highlight the seat, create textures and also some kind of branding,” Helmig adds.
Maeizo features again behind the dash, as well as on the super-slim, foldable table, while the strong but lightweight underlying materials allow for marble flooring. “You can have a real stone material, just a very thin layer: you have the surface properties and the quality, but you don’t need big [thick] tiles,” said Helmig. “It’s such a thin layer, you can also illuminate it.” The polycarbonates and films continue on the glove box cover, vents and touchpads, and polyurethane foam is a sound-canceller in the ‘privacy hood’ that lowers over the rear seats. “It’s all about the motor functionalities and light, the ambient lighting, movement of the seats, atmosphere and privacy – all that is enabled by our materials,” Helmig concluded. “It’s giving design flexibility but is sturdy and lightweight at the same time.”
Asahi Kasei AKXY
Chemicals company Asahi Kasei brought its fully drivable AKXY concept (2017), now showcasing 36 products – from a multi-layered PET/microfibre material covering the motor/inverter to sound-absorbing polyamide foams, polyacetal resin door handles, glassfibre-reinforced thermoplastic shock absorbers, polypropylene door modules, polyethylene foam headrests, and fenders from thermoplastic resin with cellulose nanofibers. It demonstrates the level of detail involved in lightweighting. “We have a focus on lightweight materials for EVs,” said manager Hideo Yoshida. “Foams and plastics; where there is normally resin, we can make it as foam.”
Foams, foils and surfaces
Chemical foaming was also seen at Pret, whose wireframe model claimed weight reductions of up to 25% in door panels, as well as blended materials saving up to 45% of weight in air vent housings and areas such as dash panels; and similar models from the likes of LG Chem and Cabot pinpointed their areas of innovation. Plastics giant Dow – supplier for components including the Range Rover Evoque’s tailgate and BMW fascias – showed seats and IPs with thinner and lighter foams, as well as promising low odours and low emissions of volatile organic compounds (VOCs). Sabic had the new Land Rover Defender on its stand, featuring its materials for the lower IP assembly and glovebox. Bplas lined up Ford fenders to show off its coatings and 3D prototyping skills. Suppliers including Merck and Architexture showed printed dash surfaces, foils and artificial leathers giving 3D effects. Proseat, supplier of seat foams and surfaces to clients including the VW Group, claimed materials with low weight, high stiffness and good ventilation properties, combining foam and EPP (expanded polypropylene).
Decorative touches and textiles
Deco panels and fascias were in abundance; Kurz claimed “design for recycling” with its IMD Pur surfaces, where an injection-moulded part is decorated with an in-mould design and covered with polyurethane. This process can produce surfaces allowing LiDAR or radar beams to pass through, as well as backlighting, and supports a ‘self-healing’ scratch-resistant topcoat; complex patterns from silk-screen printing can be incorporated. Films, coatings, high-gloss surfaces and other treatments, as well as specific coatings for LEDs and lighting applications, were further seen at suppliers including BÖ LA, Pröll, Eckart, Oerlikon Balzers and Arkema.
Of the whole vehicles seen, Sekisui Plastics – supplier to Japanese OEMs for components such as toolboxes and spare wheel housings – had a special-edition Honda S660 NeoClassic on its stand, featuring a body kit made from its foams and materials; BASF displayed the Hymer VisionVenture camper van to which it contributed interior materials and a cooling-effect paint; and Borealis and Borouge had a Nio ES8 featuring their Fibremod (plastic reinforced by second-life carbonfibre) and Daplen (recycled polyolefin) materials.
Complex issues
Attending K really drives home the complexity of the supply chain in automotive manufacturing – but also, despite some creditable innovations, the continuing degree of dependency on petrochemicals. As several company spokespeople also noted, some issues of durability, quality, heat resistance and other safety concerns remain around bio-plastics, restricting where and how they can be used in automotive applications; it is important too to distinguish between so-called bio-materials – bio-based, with (some) raw materials from sustainable sources – and bio-degradable at end-of-life (not necessarily the same).
Plastics clearly offer advantages, whether for lightweighting or for incorporating controls, lighting, communications systems and other connected technologies, and with that come new opportunities for designers. However, really smart design of the future (automotive or otherwise) will not only be about responsible choice and application of materials, nor just positioning of a product within a system of use, repurposing and re-use. It will be design which also involves comprehensive rethinking of these energy-hungry cycles of production, consumption and obsolescence, and their timeframes; and thus cultural, as well as technological or industrial, changes.