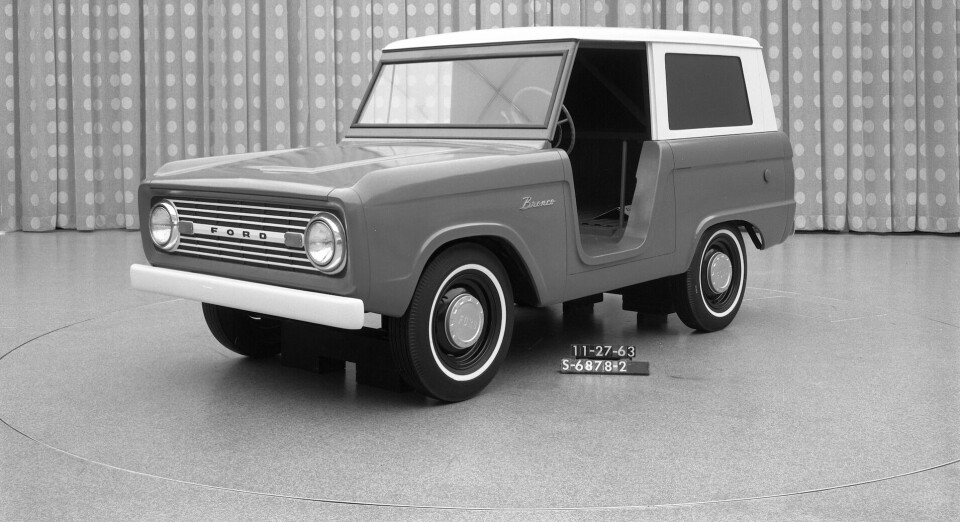
What is the future of clay modelling?
In conversation with senior designers from Audi, Karma, Mahindra and Mazda, Car Design News discussed the outlook for clay modelling as digital tools begin to play a larger role
Clay modelling has been at the forefront of automotive design for decades. Spearheaded by General Motors during the 1930s and quickly adapted by other major automakers, the process has enabled designers to create, refine and showcase physical models in the flesh.
The art of sculpting malleable clay might have evolved over the years, adopting highly accurate milling machines and often moving away from full-scale models, but the basics remain the same. Hand tools are used to shave, slice and smooth different surfaces just as they did nearly a century ago. And crucially, clay modelling’s relevance to the design process is largely unflinching, despite advances in digital tools.
“As designers, we want to integrate the best of both worlds,” says Andreas Feussner, head of modelling at Mazda Europe. “Both sides have benefits and at the end of the day, you are co-creating something. The clay team should not be fighting against the digital teams because they fear for the future of their job. It is about bringing the best of digital and clay together during the design process.” Pratap Bose, chief design officer at Mahindra Group, is of a similar opinion. “We use clay in all our studio processes. It’s still very central to what we do,” he tells Car Design News.
“The way clay is used may differ from studio to studio, but it doesn’t matter how much experience you have – you cannot skip the clay modelling process,” adds Nicholas David, interior design director at Karma. He agrees that digital tools are becoming increasingly advanced, having modelled a few concepts over his career entirely through virtual reality (VR). However, there are always things that go unnoticed when it comes to milling it out in clay.
“You see the depth, and it can make the stance of a vehicle look very different to compared to when it is in virtual reality,” David continues. “It’s a skillset that started to fade away when Alias first came out and due to 3D machining, but in my experience it is certainly coming back.”
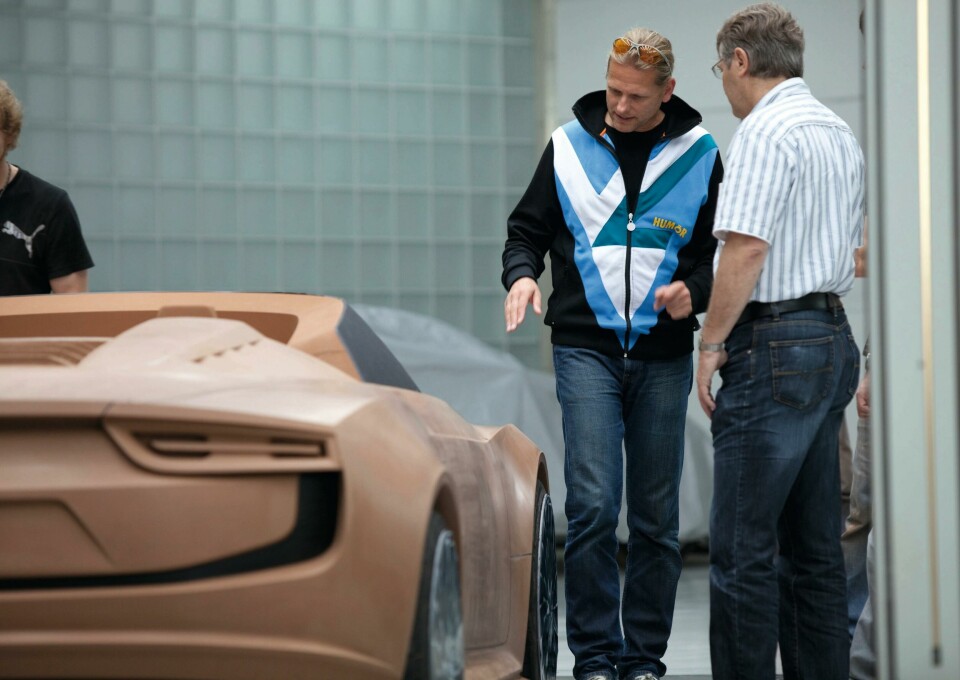
The raft of heavy machinery that goes into making a car might suggest otherwise, but car design is fundamentally a form of art. And like any artform, it is about working with one’s hands. A great 2D sketch or digital 3D model can look quite different in the flesh, and it takes a careful eye and human touch to trim, smooth or bulk out where necessary.
“Clay modellers have built up plenty of skill over the years,” continues Feussner. “We do not just slick down different surfaces; we integrate our taste into the car’s design. We are on an equal level with other designers.”
Eike Aden, an exterior designer at Audi AG, also points to the unquantifiable impact of the human touch. “Experienced Audi clay modelers create forms and design solutions that represent the Audi Design DNA. This is crucial for a car manufacturer with a long history of developing iconic cars with a persistent and beautiful design language,” he explains. “Audi customers tend to look for and appreciate the additional value of a well-executed design – enabled by our unique design process.”
Clay is part of the process but it is not the only process
This is all well and good, but it would be ignorant to discount the value of digital processes. Bullish as he is on clay models, Aden suggests they are perhaps “value-add” today in some respects. “A clay model fulfils two main tasks: enabling the design process as well as [supporting] decision making and design promotion,” he says. “But the design process is gradually becoming more digital, with cycles relying either on manual or digital input as the main source for the design development.” Today, he affirms, a combination of both fields “is delivering the best results.”
So, what does this mean in practical terms for clay teams? While it may have taken weeks to put together a clay model in the ‘30s, the process has become far more streamlined. The base of a model can in some cases be milled overnight and worked on the next morning. Smaller scale models are also cutting down development times. And with the support of digital tools, incremental tweaks can be transferred from screen to sculpture.
“Manual design refinement and form finding is now used in shorter periods than some years ago,” Aden explains. “Digital tools for creating design surfaces and for visualisation purposes are constantly evolving and have a great potential of becoming the dominant implementation in the design process, with a shortened but efficient manual clay sculpting window for a value-adding, exclusive Audi design language.”
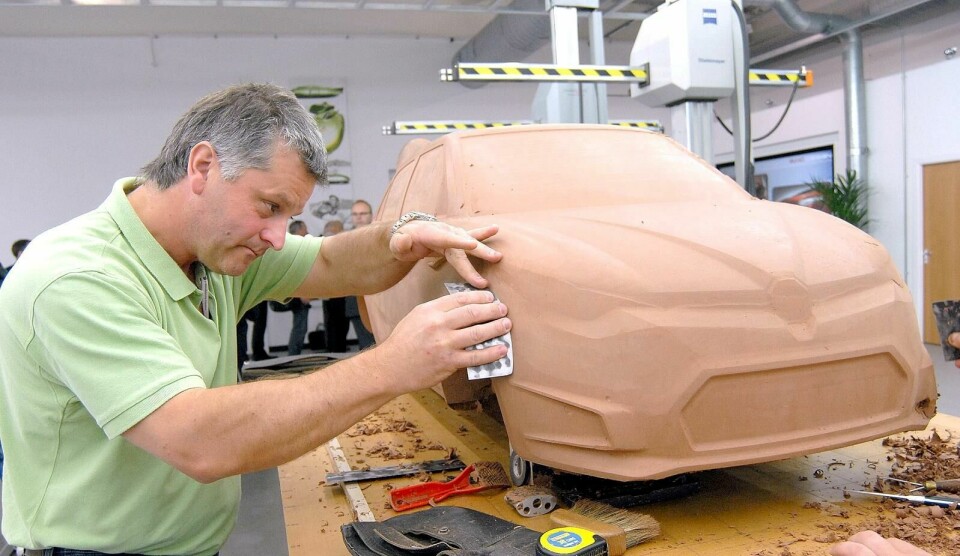
“Clay is part of the process but it is not the only process,” adds Mahindra’s Bose. “We start with a blender model, then surfaces that we can machine, and within a week to ten days you can have a 40% model in clay. Clay and digital used to be a divide, but now it is more like a permeable membrane. When I see a digital model, for example, it’s often a scan of clay.”
Digital tools, then, are playing a greater role in the design of a new vehicle. However, the next generation of students recognise that clay modelling will remain a vital skill – even if they eventually land a job in a digital studio. And vice versa. Speaking with nearly 20 students from Coventry’s automotive design course in the UK earlier this year, the general feeling was that any designer worth their salt must be well-rounded regardless of their speciality.
“The upcoming generation of clay modellers is educated in both worlds,” agrees Mazda’s Feussner. “For them it is not just clay modelling, but hybrid models. We are happy to have these guys on our team because they know physical modelling and fabrication, but also have the digital skills and understand how to bring it all together.”
A physical model will always be an extremely valuable tool… Whether that needs to be in clay is a question that each OEM has to answer for itself
Martin Groschwald, Managing Director at Konzepthaus Design, agrees that hybrid models may well become the new normal. This is no death knell for clay, but more of an expansion of the role.
“For the vast majority, a physical model will always be an extremely valuable tool to evaluate models in a real-life environment. Whether that needs to be in clay is a question that each OEM has to answer for itself,” he observes. “You might see some exceptions where cars are almost entirely done in 3D – Bugatti has been very advanced with this method – and only use a verification model. But on the grand scale, I still believe that clay and physical models will continue to be an important part of the vehicle design process.”
And so despite an unrelenting march toward digitalisation, the analogue processes that first underpinned car design look set to hold true. Senior figures in this field point out that a finely-tuned digital model today often results from a scan of a carefully sculpted clay model, and vice versa. These are not two conflicting fields of study – in the way that interior and exterior teams once were – and are in fact complementary practices.
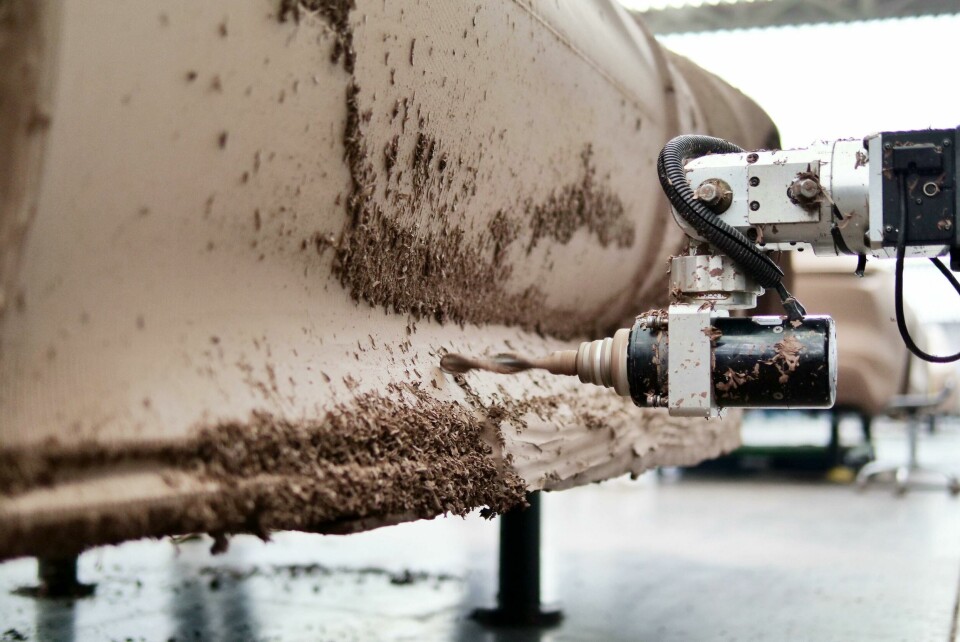
“Clay is still very important at some traditional manufacturers, no matter which type of car they are working on,” observes Oliver Vogt, Partner at Konzepthaus Innovation Consultancy. “But nowadays, it is used much later in the process and has more the role of a verification tool to refine the design intent.” The general trend has been to avoid full-sized clay models in recent years, and this is likely to continue. That being said, a 1:1 hard model, typically fibreglass, is always needed for final management sign-off, he adds.
Karma’s David concludes that this is not the first point in time where the role of clay modelling has come under question. “Even when I was in college, I thought clay might eventually fade out. But from my experience in the industry so far, I definitely think it will still be around in decades to come. Technology is constantly improving, but unless there is a huge leap that makes VR absolutely realistic to the point where it is life-like, clay will still be around.” Car Design News will be digging deeper into the world of clay modelling, which appears to have a bright future despite concerns of digital design domination.
Are you a designer? The CDN People Awards, which celebrates the people behind the design, presents an opportunity to champion the clay modellers in your team. You can enter for free here, and the deadline for submissions is 25 August 2022.