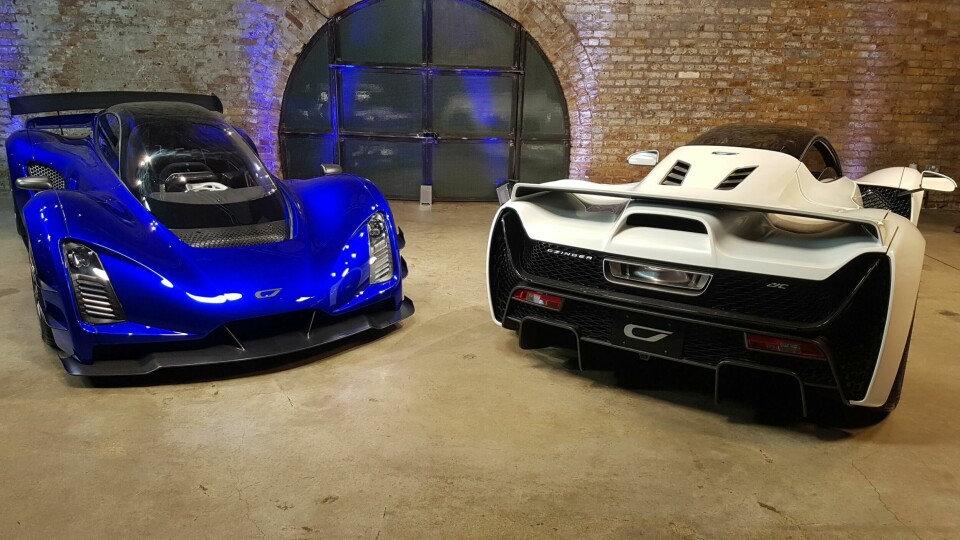
Czinger’s Design Director on the 21C
David O’Connell tells CDN about the 21C and the potential of the company’s unique approach to design and production
There are many new supercars and hypercars with headline-grabbing four-figure power outputs, lots of accompanying chatter about striving for light weight through use of advanced materials, and usually some form of electrified powertrain. None of them, however, are quite the same as the Czinger 21C. Far from a straightforward us-too supercar start-up, Czinger has reimagined car production and based not just their car but their whole factory around two key technologies: generative design, and additive manufacturing. The results were, finally, put on proud display at the international launch in London earlier this month. CDN was there, and spoke to the LA-based company’s affable chief design officer, David O’Connell.
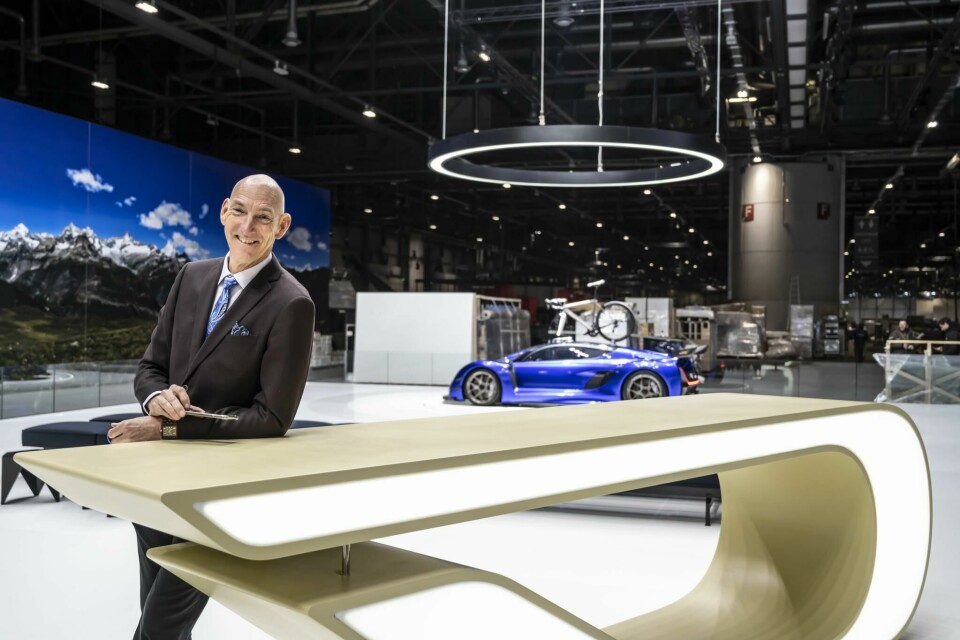
One important thing to note at this stage is that the exterior design has been predominantly done through conventional processes, including good ol’ clay modelling. “Our philosophy is that we are only printing the complex structures of the car. It doesn’t make sense to 3D-print the whole thing, so you print these areas that are structurally complex like the suspension parts and the pillars, and the rest is carbon or aluminium sheets which are very efficient and effective in what they do,” O’Connell told CDN. “We’re really not there yet with [printing] exterior Class-A, or wheels. Are these things to be explored? Of course; printer technology is rapidly expanding and so those are in our sight.”
On display were two different ‘trims’ of 21C: a road version in ‘Wild Orchid White’ and a track version painted in a deep, clearcoated sapphire hue dubbed ‘Blue My Mind’. Aside from the track car having much larger bare-carbon aero parts, the main differences in design are down to the CMF and different wheel styles.
“I think, if you take this vehicle and put a car cover over it, it really looks nothing like any of the other hypercars that are being made, observed O’Connell. “I have so much respect for the competition, they do beautiful things, but I think one thing that we have over them is that there’s a newness about this proportion and a newness about the whole approach to the car. We’re really excited about what lays ahead with these foundations.”
While Mr. Czinger referenced fighter jets and associated imagery (SR-71, Top Gun, Chuck Yeager and Star Wars pod-racers) as design inspirations, the very low nose – with stacked all-LED headlights and highly pronounced, curvaceous front wheel arches – was also inspired by the front of a Lola T70 endurance racer. What’s more, from the side, that long, 1+1 seat cabin’s smoothly arching silhouette was created in the image of a katana. “We took a lot of inspiration from the profile of a samurai sword, with a single-curve blade,” commented O’Connell. “This car is made up of several curvatures, but the overall impression is that it’s very simple and pure.”
This impression is made stronger by a mission to either eliminate or hide shutlines, as he also explained: “Every graphic element – headlights, scoops – are all for a reason, they’re the size they need to be, but what I think is very cool about the execution is that there’s a cutline that connects each one of those graphic elements, which I think adds a lot of rationale. We call it ‘line logic’. If you look at the bodyside, it’s all done in one piece, so there’s no extra cuts or separations of form.” As such, the six-strong design team fought to ensure, for instance, that the DLO on each side remained as a single piece of glass that can fully disappear into the long, single door, with no B-pillar breaking it up into sections.
The rear end is effectively completely open to channel airflow and ventilate heat. Aside from a U-shaped strip of red LEDs spanning the tail and the vast air diffuser below it, the rear end comprises of a single grille piece that twists and changes density as it reaches into the bodywork at the top. On the road car this is 3D printed (as is the little grille at the base of the windscreen), but on the track car it’s CNC machined carbonfibre just 3mm thick, to shave off a few vital grams. Atop all of this, on both cars, is an integrated spoiler which sits over two deep air channels to activate the underside of it. “We just kept diggin’ away at the clay until we hit something hard,” said O’Connell of creating these channels, either side of the engine heat chimneys at the end of that katana profile. The central exhaust outlet is 3D printed (in Inconel for the track version) and spits flames in a cross-flowing ‘X’ shape. Which is fun.
“What I really love on the car also is: look at the A-pillar and the way it comes up, up the side of the car, across the top of the wheel, then it goes rearward across the canopy [and the engine cover], then it turns in plan-view and becomes the leading edge of the wing,” observed O’Connell. “So, it’s got a very cool three-dimensional character to it. That, combined with the simplicity and purity of that cabin, with that signature line logic, and the inline seating? Put the pen down. You’re done! You’ve got it.”
– The first image shows all the 3D printed components in blue
The ‘pure’ carbonfibre skin creates a strong juxtaposition against the mechanical components millimetres beneath it, which are immensely complex and intricate in shape. A component they’re particularly proud of is the hollow, biomorphic-looking suspension upper control arm, which when you hold it feels for all the world like it should be made of foam or thin plastic, not metal – save for the cold hard texture on your fingertips. Yet it’s strong enough to do its job.
It’s the engineering-led components where generative design and additive manufacturing really come into play on the 21C – but not all of it is hidden. “In the course of developing this car we grappled with how much of the 3D-printed story we wanted to tell,” said O’Connell, “but then it goes back to the form-follows-function thing of, if it’s not the right material to have on the outside of the car, don’t do it. We looked at bringing more of it out, but it didn’t make sense from a performance point of view, and it started conflicting aesthetically. So, it’s always about what’s the right answer for the right question.”
There are hints large and small to find, though. One clear example is the structural piece over the steering column, visible through the windscreen. “That is 100% design working with engineering to achieve that success,” explained O’Connell. “That’s a perfect example of that meshing of those two worlds for a totally successful design. We call it the storefront to the interior, because when you look through the canopy, that’s what you see – and there’s no denying what it is or what it does, but at the same time it’s like ‘wow holy shit look at that thing, it’s really beautiful’!”
The steering wheel is a single printed piece, wrapped mostly in suede. Its exposed lower section has the same look to it as the generatively designed suspension components – like a plant root made of metal (the two launch cars feature different iterations of this idea here). “Again, that’s a great example of an optimised set of performance shapes, very cool and fresh, against natural material, and there’s not a gram of material on those components that was added for aesthetics. It’s great because everyone’s happy,” O’Connell enthused. “The beauty in a lot of this is the componentry in itself; it’s really great industrial art.”
However, it’s no guarantee that the generative software will spit out a shape that works for both design and engineering teams every time – as we touched on with BAC earlier this month with their crazy-looking brake calliper. “Sometimes they’re not the prettiest in the world,” admits O’Connell equally, “so that’s where you have to work very closely with the reality of that execution to make sure you’re not adding more weight [for aesthetics], compromising the purity of the part – but it also depends if somebody is going to see it or not.” That final point is of course why the upper control arm, normally hidden behind the wheel hub, can look all wild compared to major exterior parts.
While the car technically has two doors, the door on driver’s right is the preferred side (the left side is more for “emergency access”). This is reinforced ergonomically by the HMI screen being offset to the left, which would make ingress on that side much trickier. Like a lot of high-performance, track-biased cars, getting in and out takes some strategic manoeuvring compared to an everyday car, but once you’re in, it’s a comfortable position – even for the rear passenger, who can slot their legs either side of the front seat and is treated to their own screen, complete with an adjuster function to move the seat in front of them if they’re struggling. To save space in such a narrow cockpit, every function is accessed by that portrait screen, although controls normally found on column stalks (lights, wipers, etc.) are also integrated onto the steering wheel as physical buttons. An all-digital IP is situated behind the wheel as you’d expect.
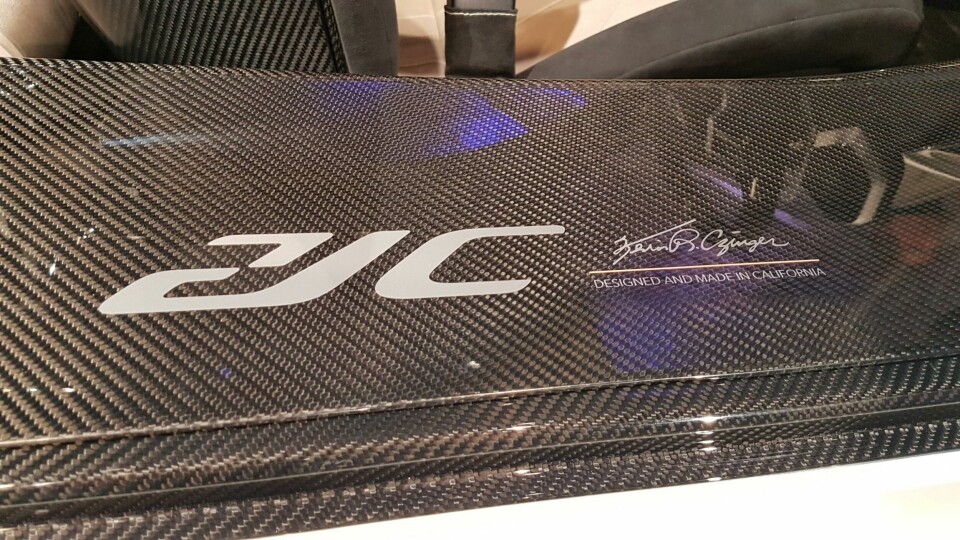
As well as conceiving the car itself, Czinger’s setup at their LA factory boasts a highly compact, scalable and adaptable production system. 3D printers print whatever they’re told to print, essentially, and so they can change what components they’re producing simply by loading a different file into the programme that runs them. What’s more, a 15x15-metre unit of computer-controlled robot arms can take care of the entire assembly process in similarly adaptable fashion; no need to re-tool a traditional production line or move machinery around. O’Connell remarked that the Divergent-Czinger system “just makes it all so easy in a lot of ways. We have a philosophy of no bracketry, so if you have a part that needs a component on it for attachment, you don’t have to weld it on, you just [add it to the CAD model] and integrate it. That’s actually a huge frontier that we’re exploring, that will minimise part count. So, it’s a whole new chapter in the book of how to make high-performance cars – and nothing’s wasted.”
Their current facilities technically have the capacity to produce as many as 10,000 chassis a year, as opposed to the 80 hypercars they’re starting with. While the 21C sets the benchmark, we could yet see something more mass-market further down the line which makes use of the system’s functional advantages to a greater degree.
“Because we’re a new brand, you get the chance to make a great first impression, not just with the aesthetics and functionality/performance. It’s a little bit of a double-edged sword, y’know; you’re not handcuffed to anything else, right, but you’ve got nothing to fall back on! But at the same time you have this great opportunity to go totally forward. For us, our horizon, we can get there because of the magic that this technology represents, and the fact that we are small, very agile. Being the pioneers of this is certainly a great asset of that program for not just myself, but my entire team and the entire Czinger brand, having this at our fingertips.”